自動化と手作業
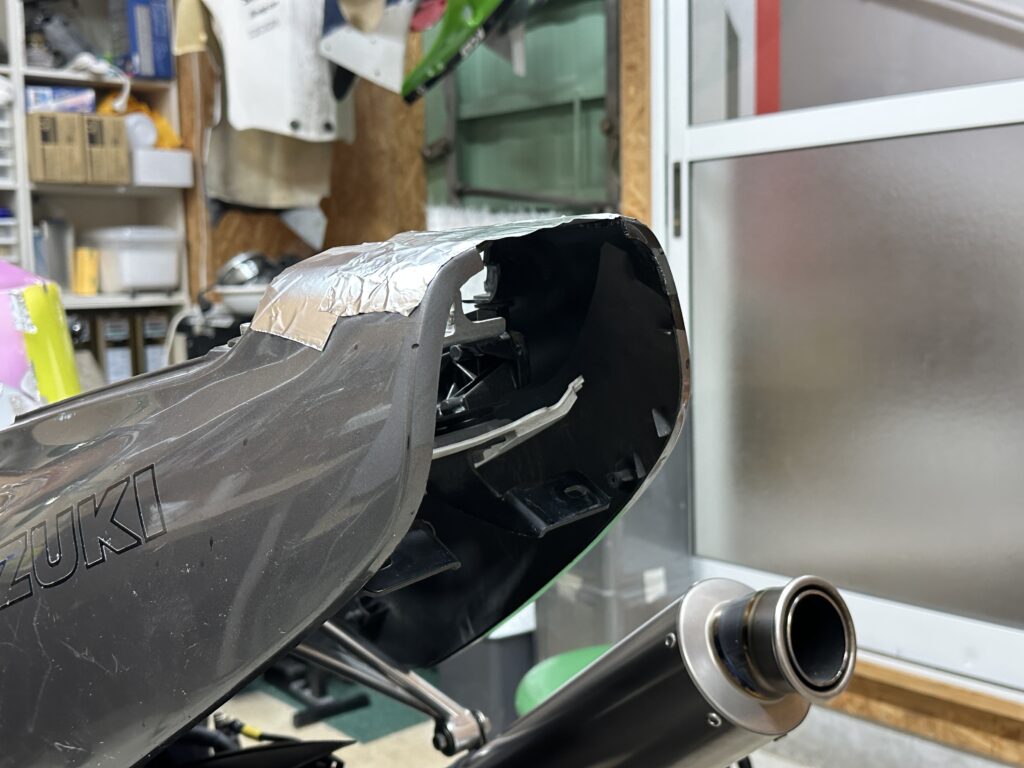
80年代、三次元曲線だらけのある種「無駄」なフォルムは、私たちを大いにノスタルジックな気分にさせてくれますが、それを加工するとなると話は別で、中々答えの出ない難題となります。
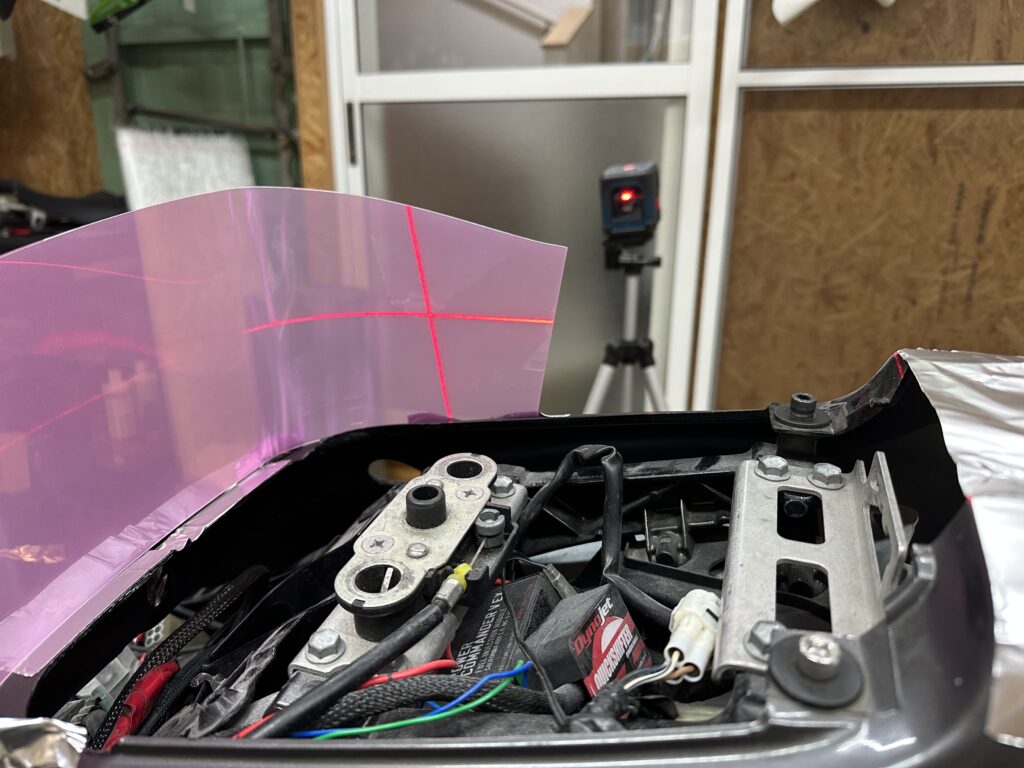
レーザー墨出し器を使って、出来るだけ曲線をカットし、ラインを見極めます。
局面においての水平出しは、ラインが歪みまくるので、これが無いと永遠に答えが出ません。
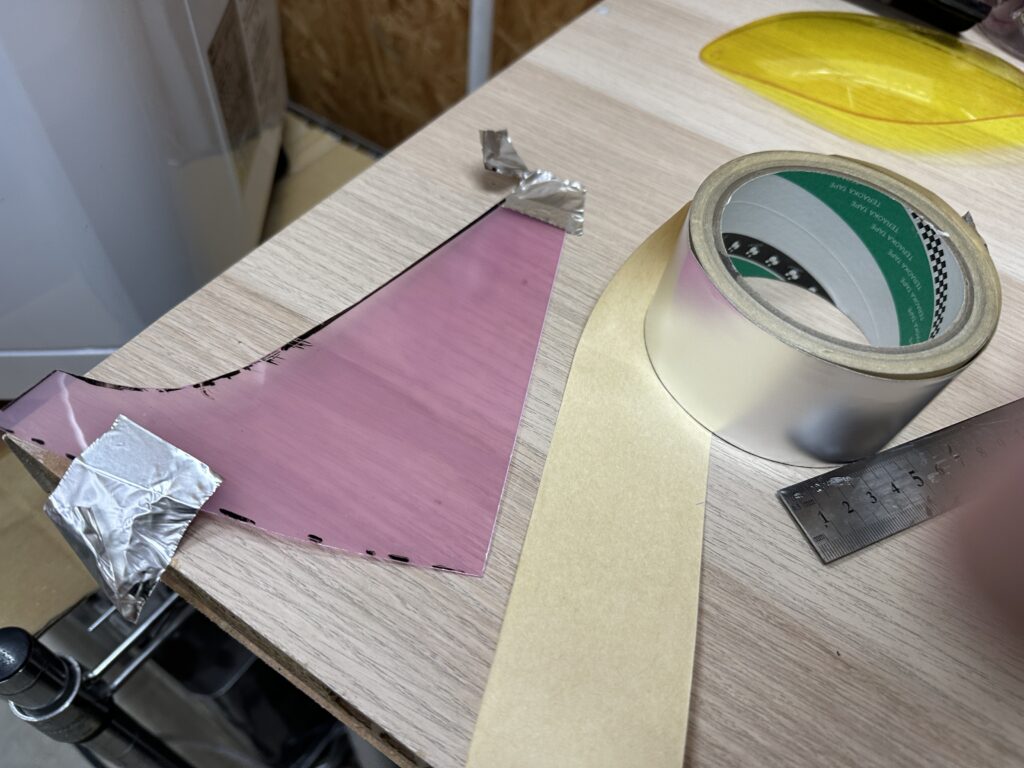
「ほんとにそんなラインなのか?」と半信半疑な気持ちのまま、PP板をカットしてゆきます。
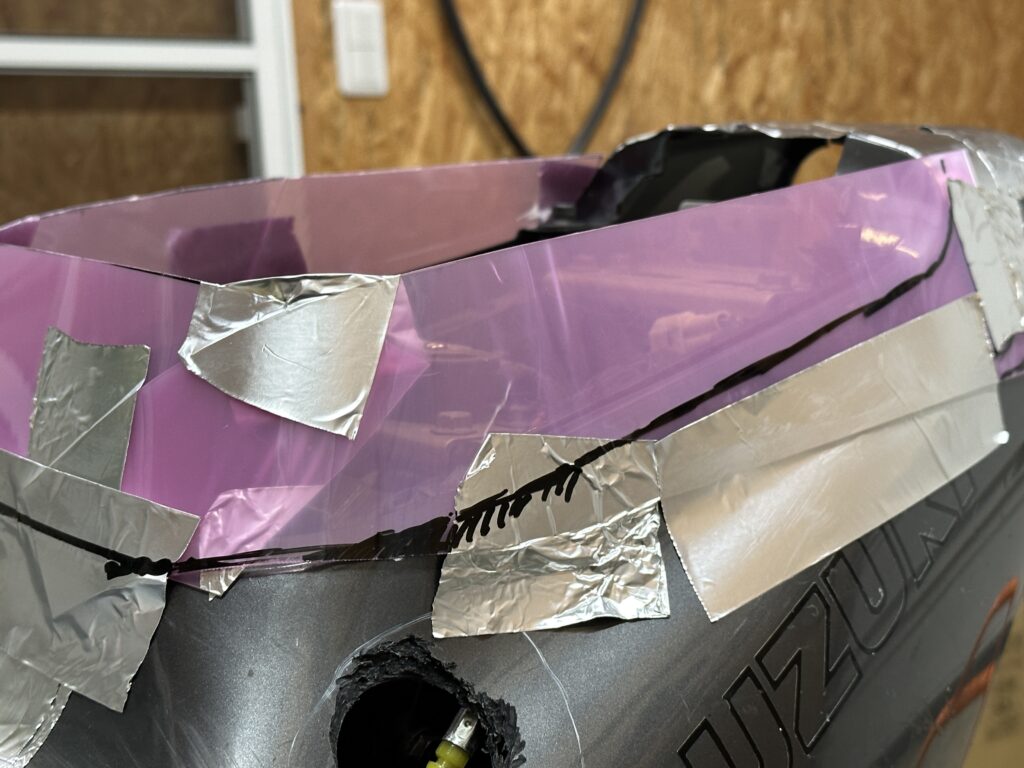
PP板は面に対して垂直方向には曲がりますが、二軸三軸では同時に曲げられません。
そのため、何枚か重ねて張り合わせることで理想の形を見つけるしかありません。
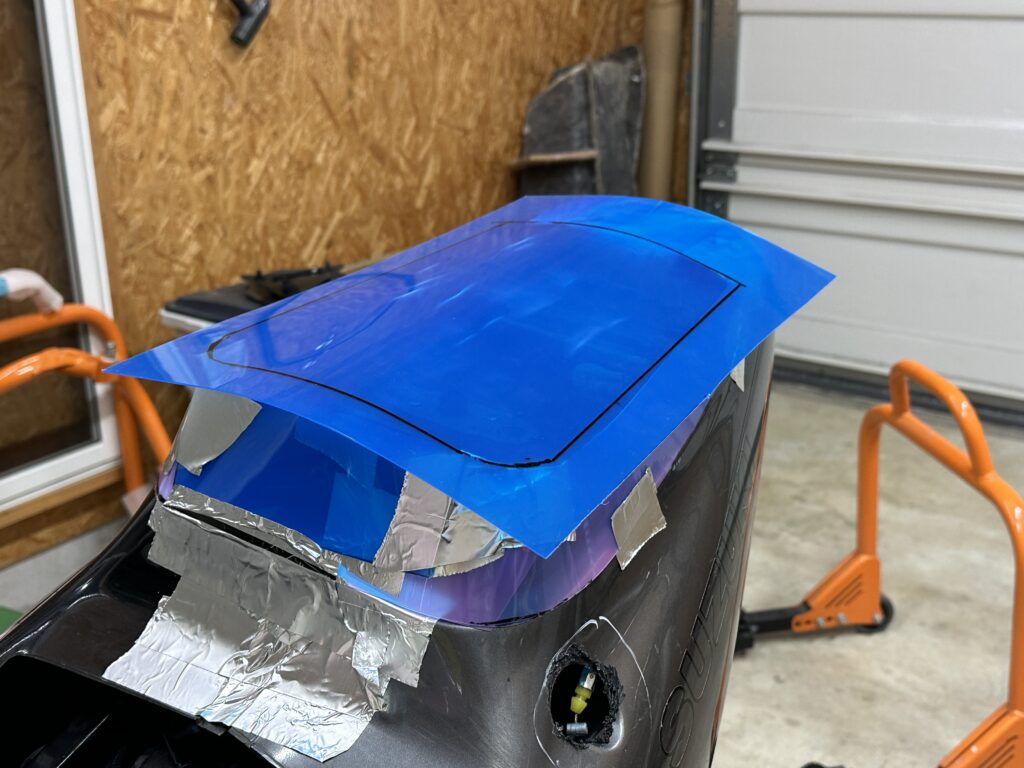
クラシック真っすぐなところなど一つもありませんので、天板も曲がりまくりです。
真っすぐな面をFRPで作るのも、それはそれで大変ですが・・・(笑)。
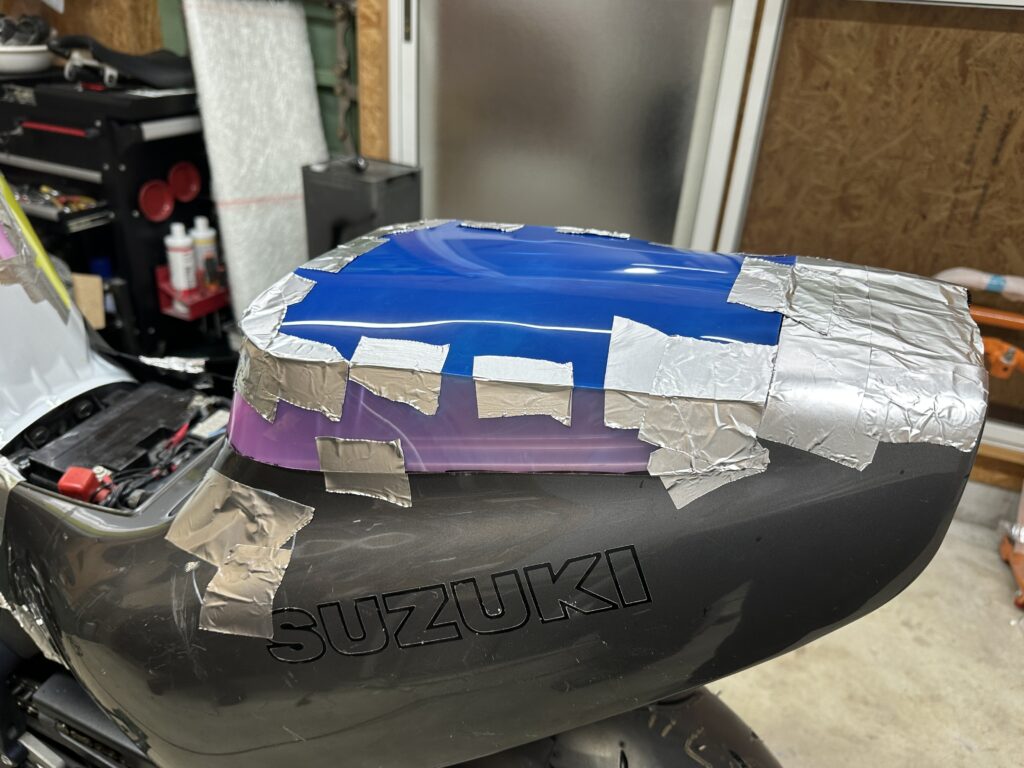
この辺の面出しは、型で一発で追い込もうとはせず、作ってから削って合わせた方が楽なので、意図的に適当に作ってしまいます。
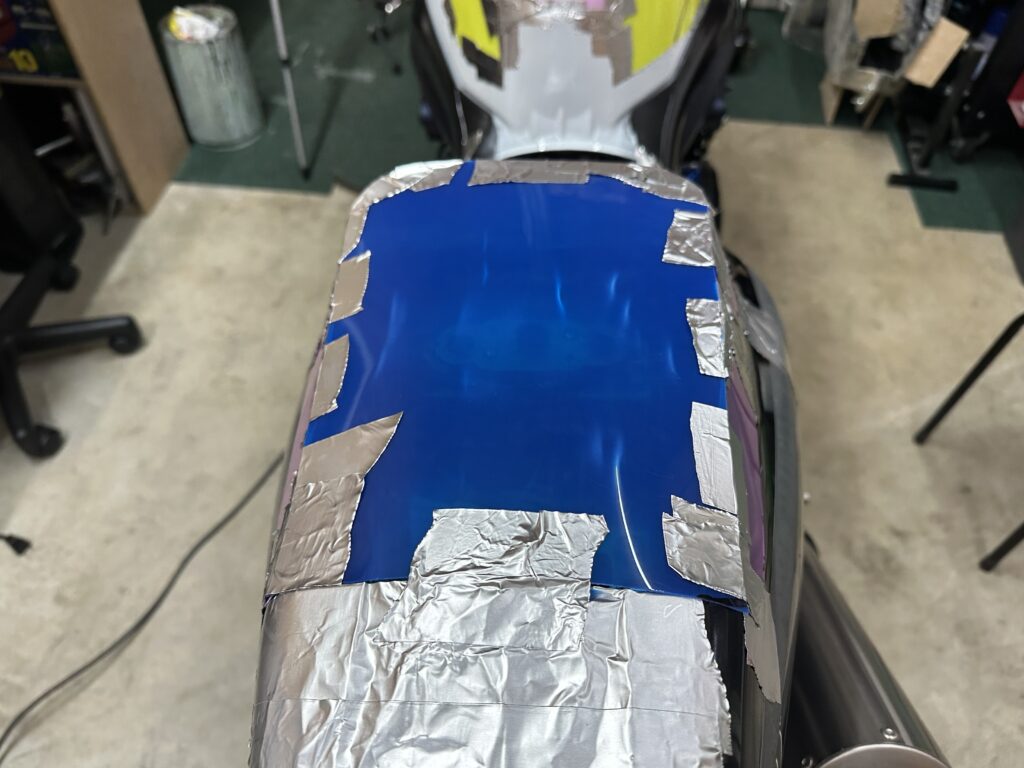
一度作ってしまってから車両にセットして固定した上で、マスキングしてからパテで面を整える方法を模索思案す。
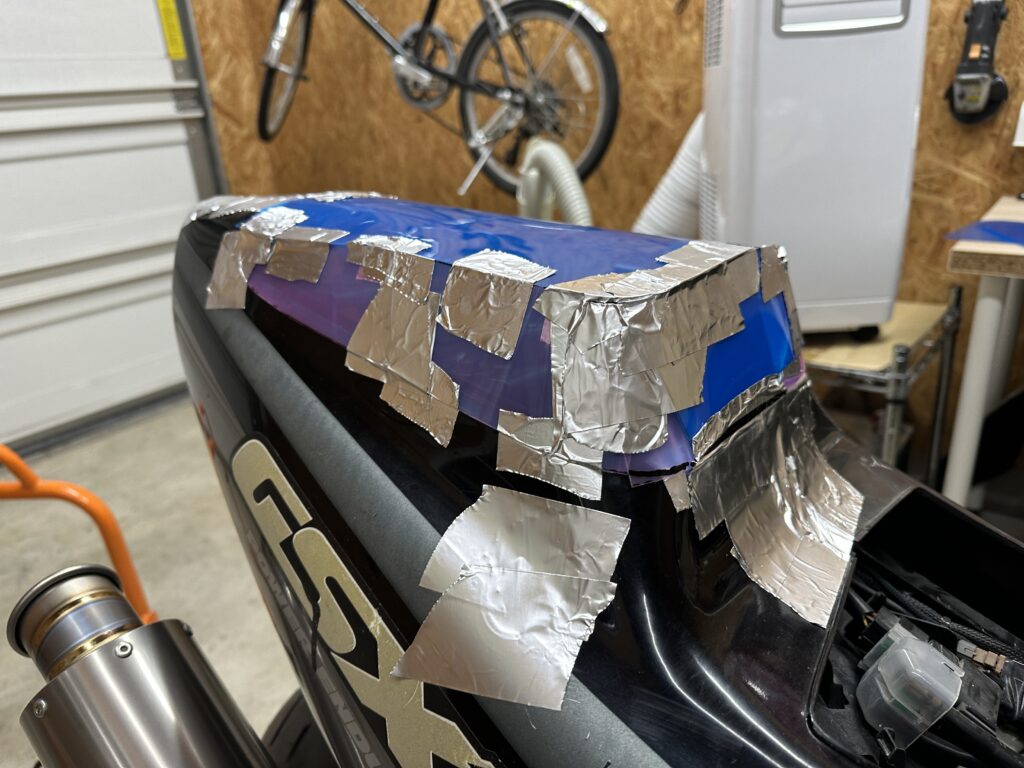
高さを整え、タンクとの水平なラインを意識します。
純正のシートキャッチを活用して、ワンキーで開閉可能なシングルシートカバーの作成を目指します。
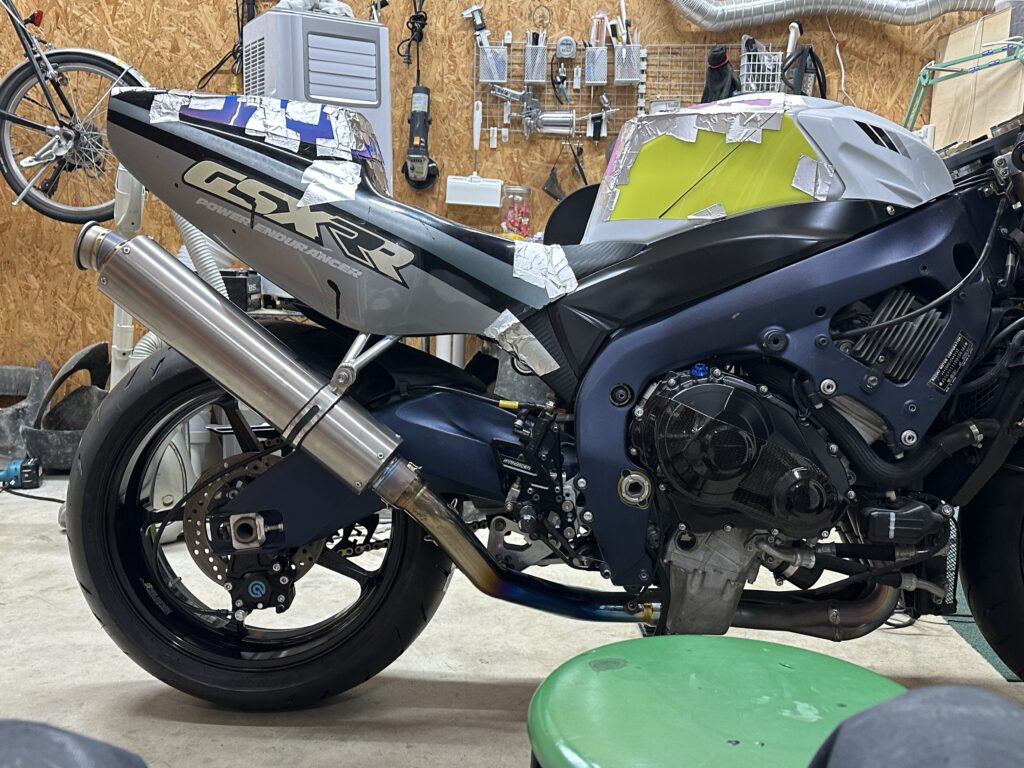
ストンと落とし穴の様なシート位置が出てきました。
一つの部分が形になると、良いところも悪いところも一気に見えてくるのが何とも面白いです。
妥協しないため、全部壊してやり直したりします。
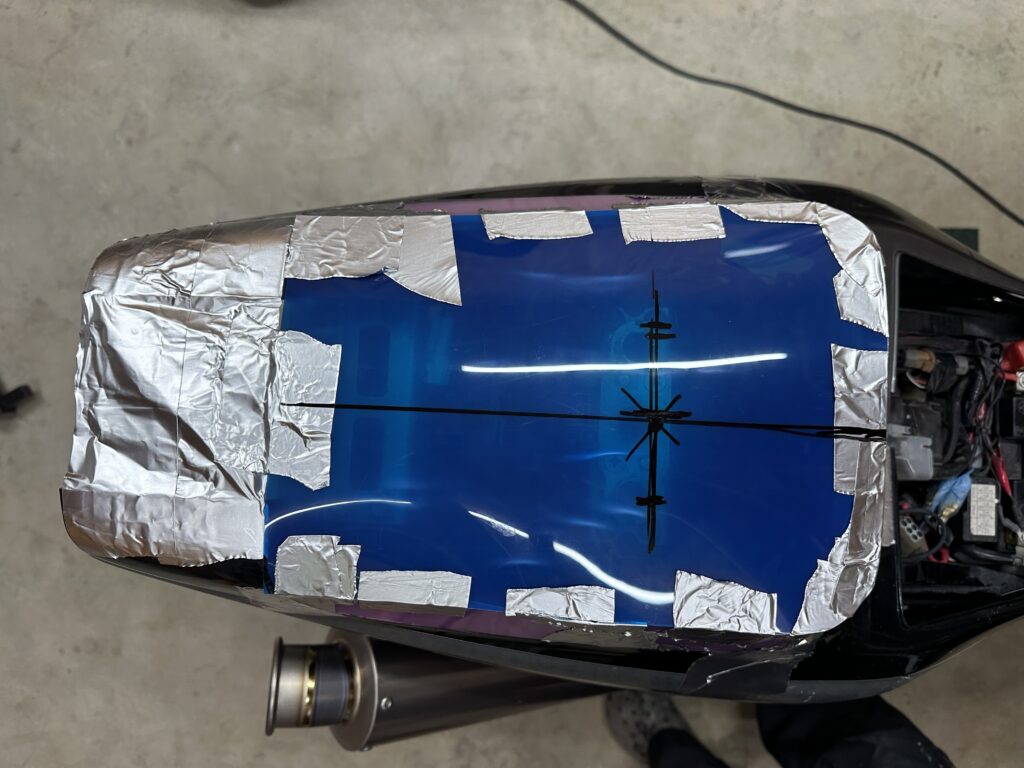
この段階までプロトタイピングすることで唯一解ることが一つだけあります。
それはシートキャッチの固定位置出しです。
カウルスワップは、一から十まで位置出しの奴隷となります。
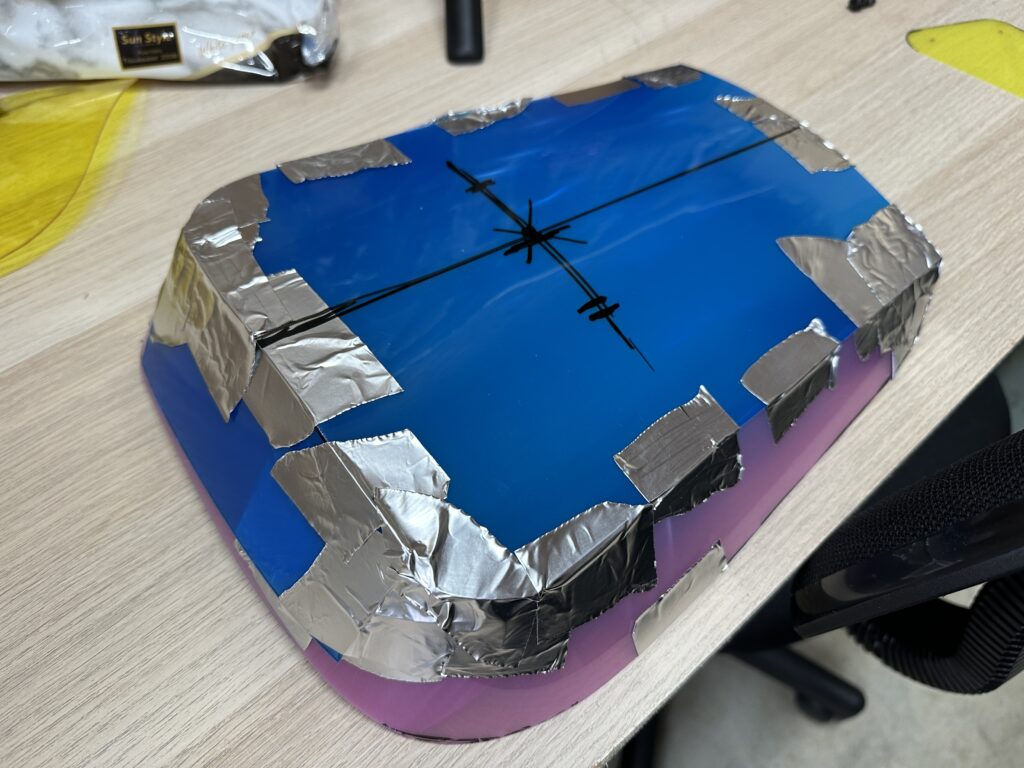
かなり精度の低い原型が出来ました(笑)。
これを元に紙で型紙を取り直した上で、もっと頑丈な厚みのあるPP板を切り出しながら、更に精度を上げ型を作ります。
FRPの張り込みまでは、まだまだ沢山の超えなくてはいけないハードルがあります。