リバースエンジニアリング1:シングルシートカバー
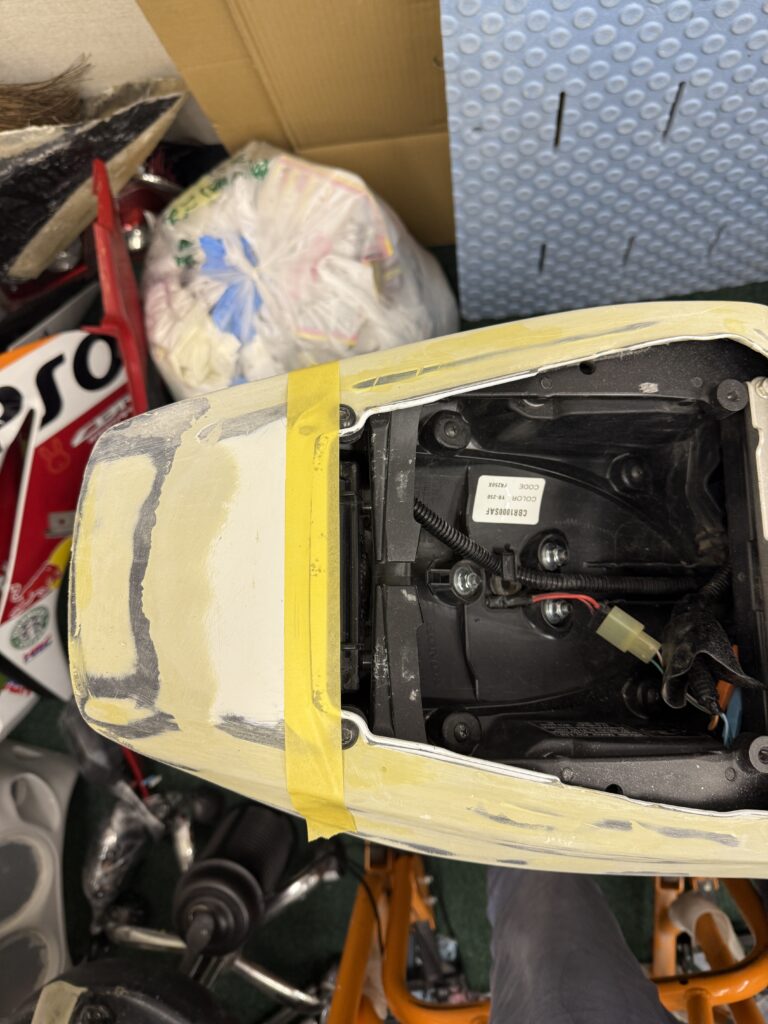
シート形状を少々変更します。
段付き構造にするためにも、脱着用のボルト位置も含め、どこら辺までがOKなのか?
目分量でしるしをつけておきます。
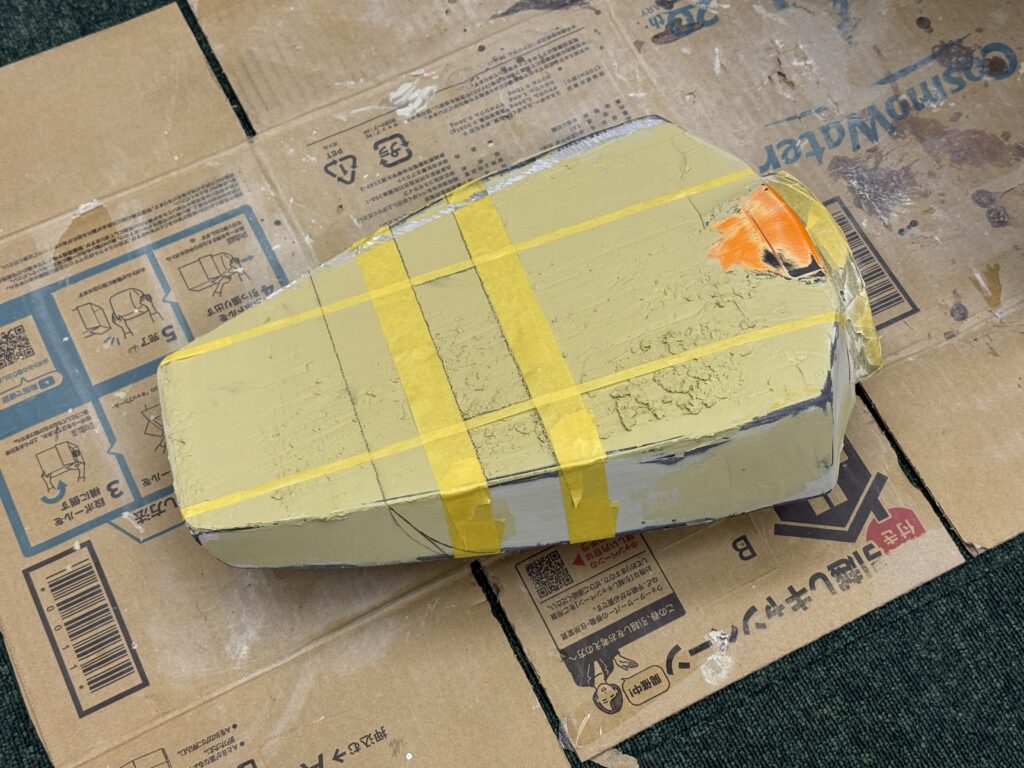
鉛筆で大まかにしるしをつけておきます。
既に合体済みですが、前後の脱着に必要な機構は、この状態から救出する必要があります。
既にガッチリと結合させてしまったので、これは一苦労です。
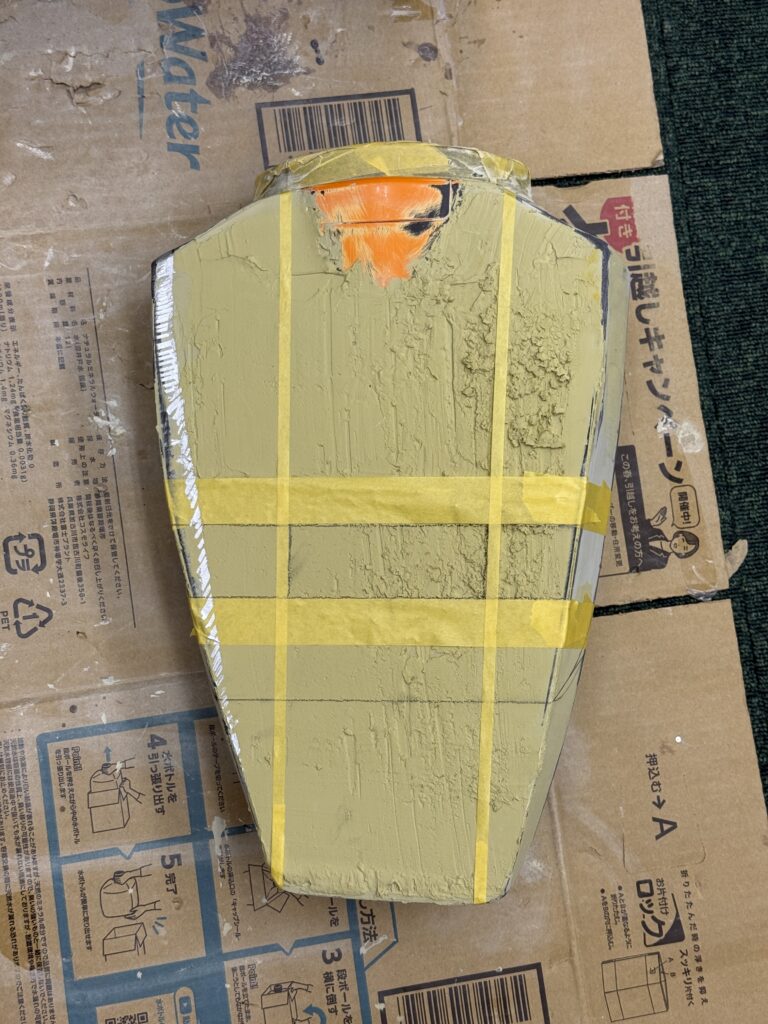
こうなったらもうどうでも良い事ですが、左右対称であれば最低でもこのラインだったはずです。
折角作り直すのであれば、今度こそ完璧にします。
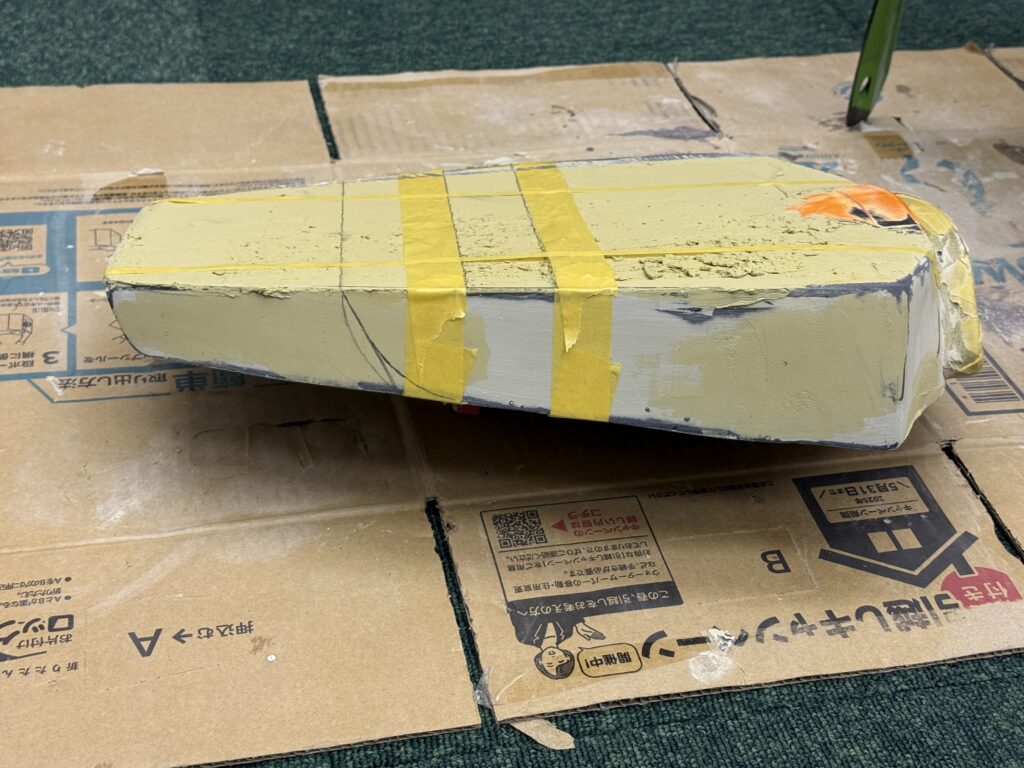
おっと・・・・また少しズレそうだったので計測してラインの引き直し。
危ない危ない。油断も隙もあったもんじゃない。
リバースエンジニアリング2:シングルシートカバー
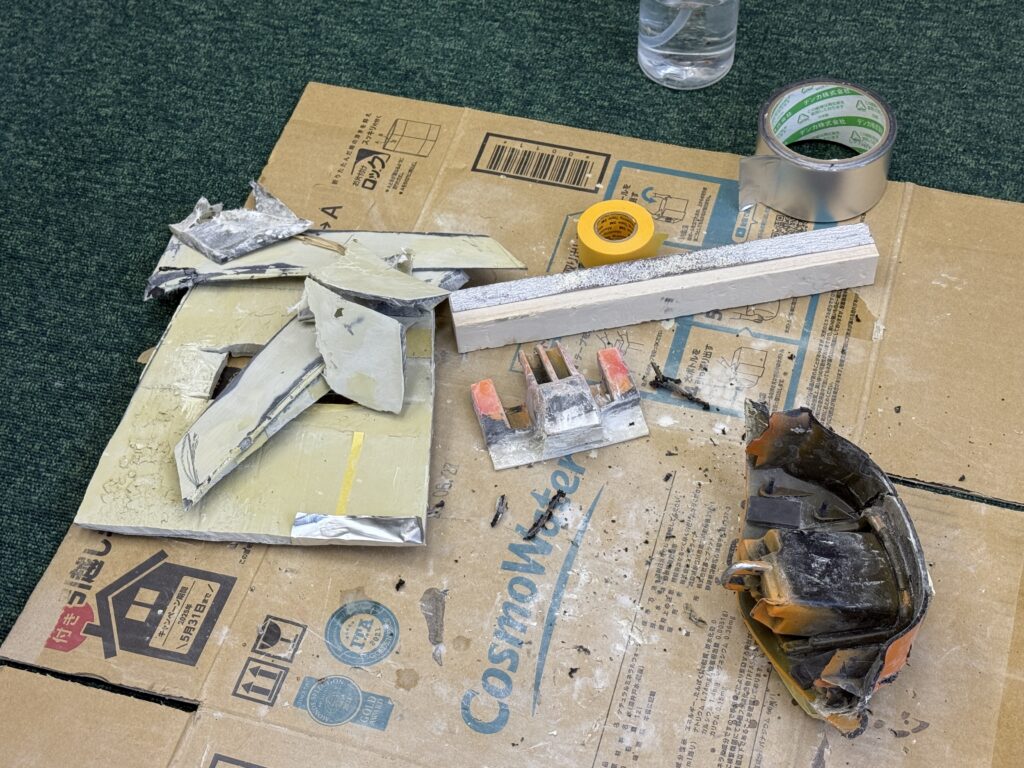
泣きながら電動ソーを振り回す事20分。
作るのには一週間もかかったのに、壊すのはあっという間でした。
何事も無かったかのように綺麗に取り出された部品たちが、逆に哀愁を誘います。
時計の針が巻き戻った気分です。
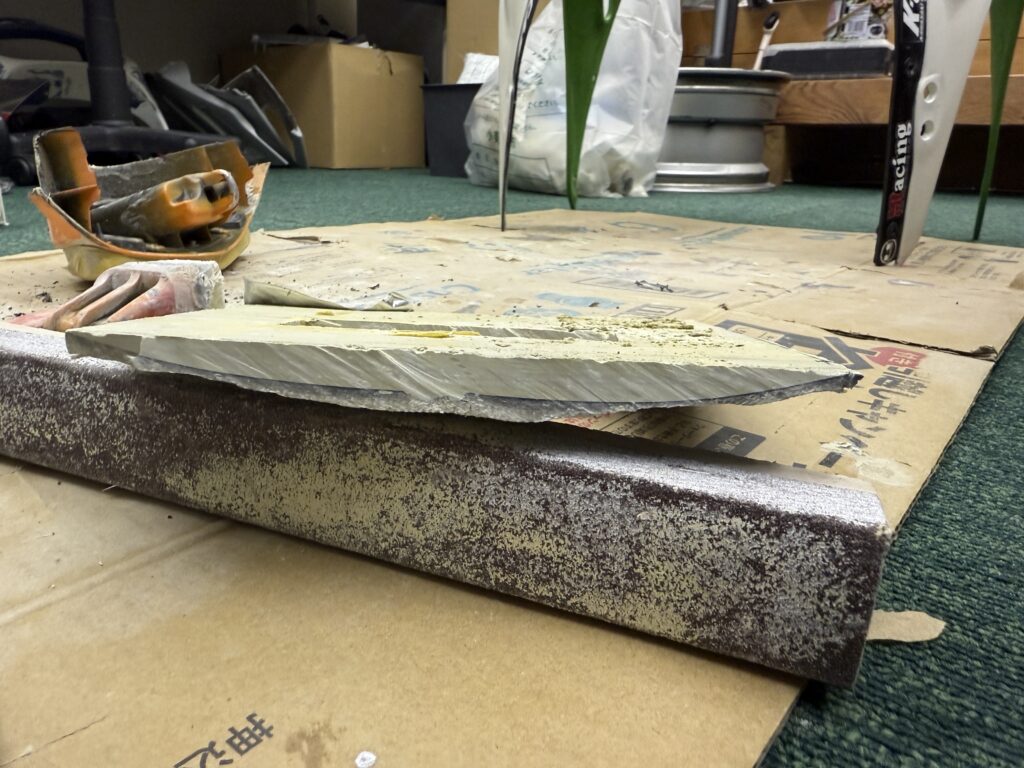
天板切断面アップです。
これだけパテを盛ったら、そりゃ重くなるでしょうって話です。
事実、片手でひょいと持つには、ちょっと抵抗があるくらいの重さになっていました。
今回のようなことが起きなくても、作り直しで良かったのかもしれません。
これで良かったんだ。
今はそう言い聞かせています。
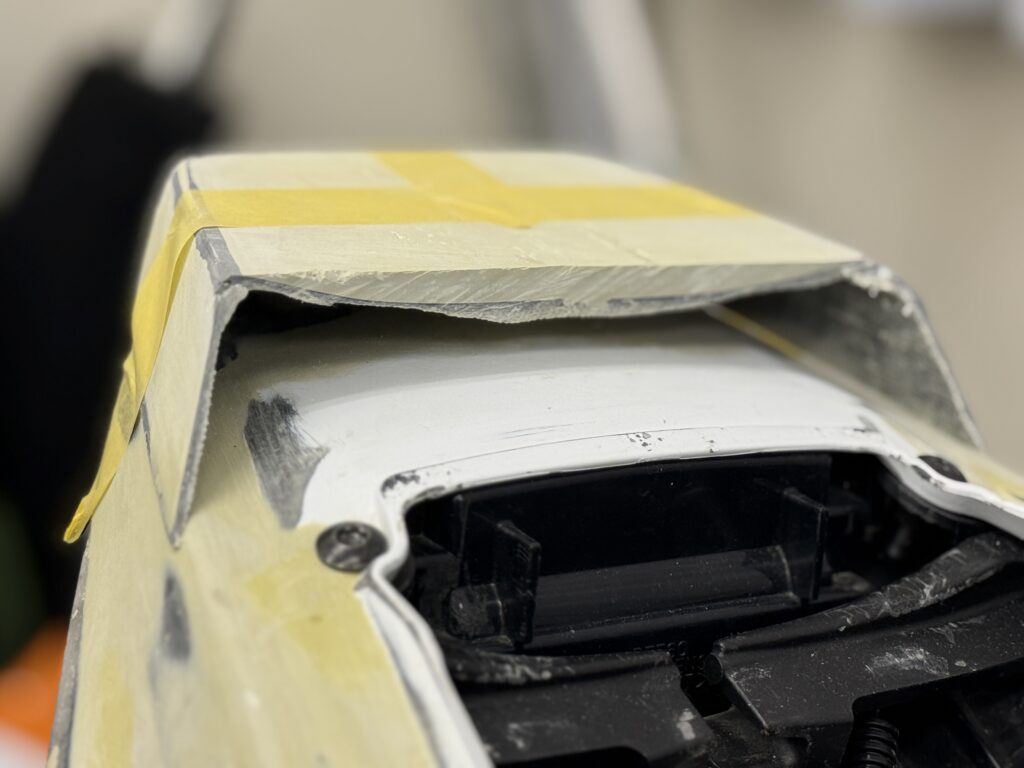
カットしたカバーの一部は勿体ないので流用します。
シート形状をここだけ段付きにして、蓋をして埋めてしまいます。
シートカウルはマスターモデルとして、型を取るのでいくら重くなっても製品には影響しません。
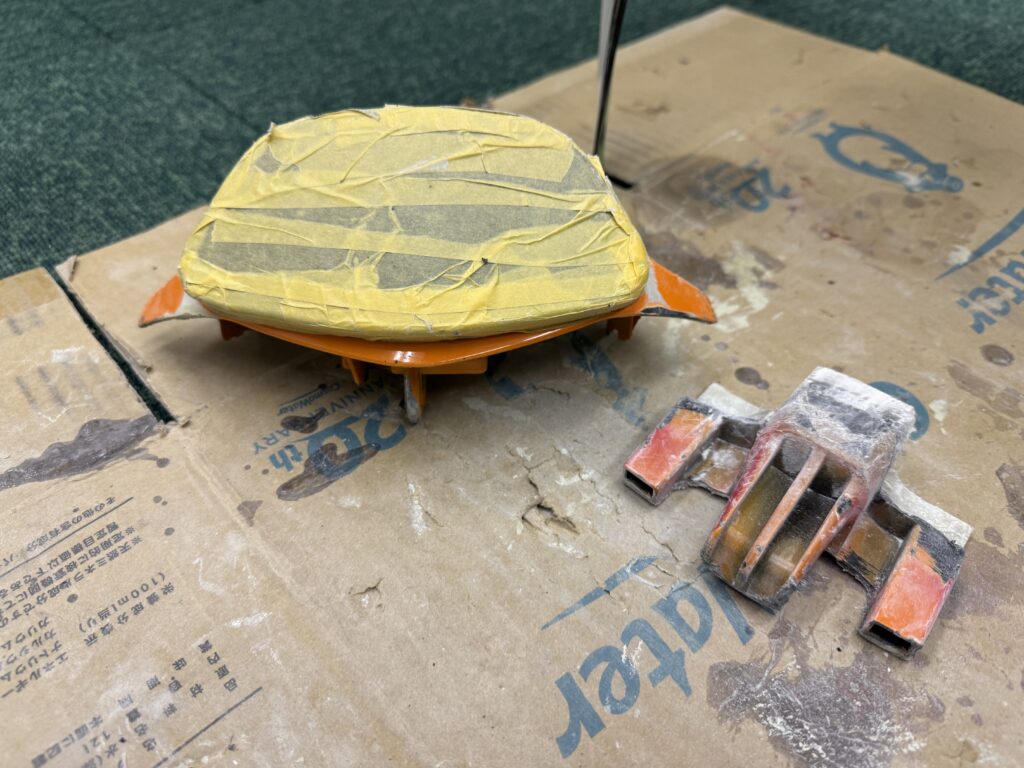
重要なパーツたち。
逆にこいつらが複雑すぎてコピーできなかった。
何とかならんもんかね・・・・往生際の悪い私です。
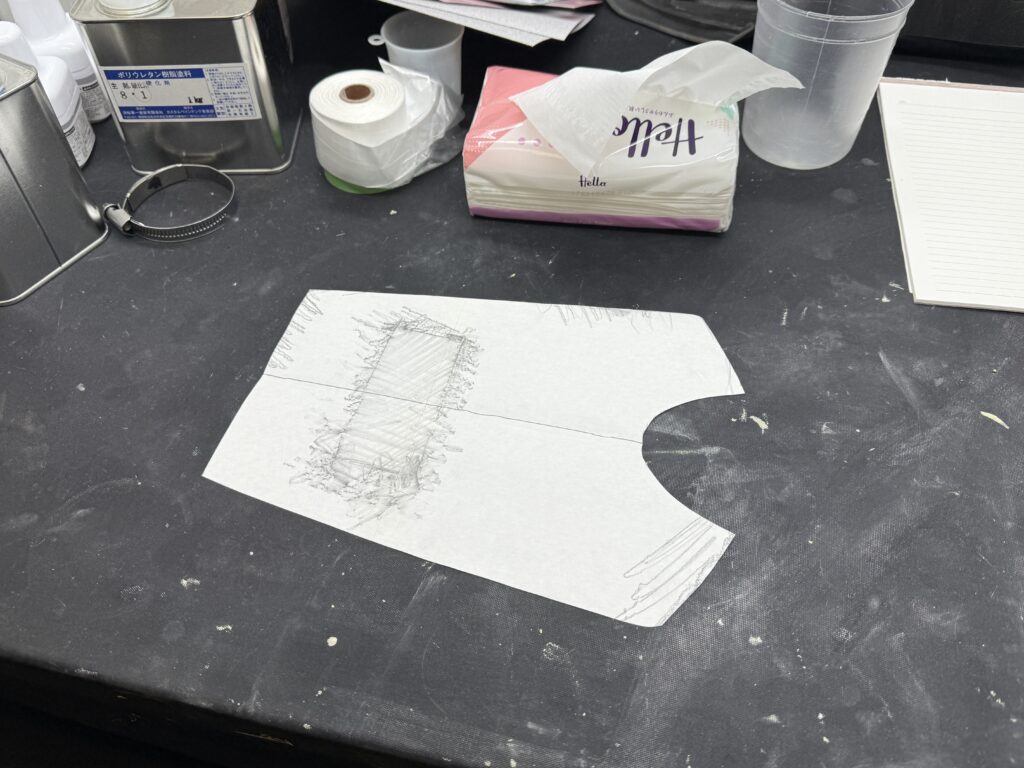
気を取り直して、歪んでいない理想的な天板形状を、予め型紙で作成しておきます。
今回は二度目なので、金具の取り出し位置まで先に分かっていますので楽です。
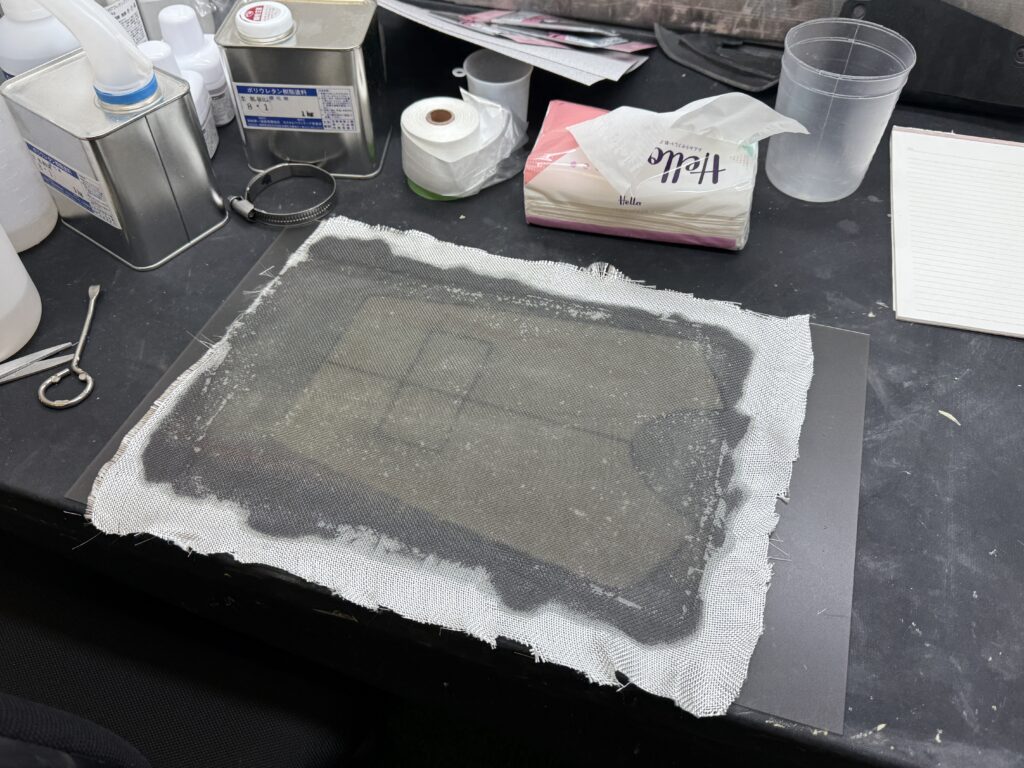
PP板を平らな所に敷いたら、その上でFRPを含侵し、真っ直ぐなFRPの板を作ります。
これはカーボンの板を作るのと同じ工程です。
余談ですが、この方法にひと手間加えるだけで、ウェットカーボンでよければ、ライセンスプレートなどのカーボンパーツが作れます。
予め型紙を下に轢いておいたので、透けたPP板にはマジックで形を上からなぞって書いておきます。
その上に樹脂を塗って築層するので、マジックがそのままFRPの表面にに写るので、後でカットしやすくなります。
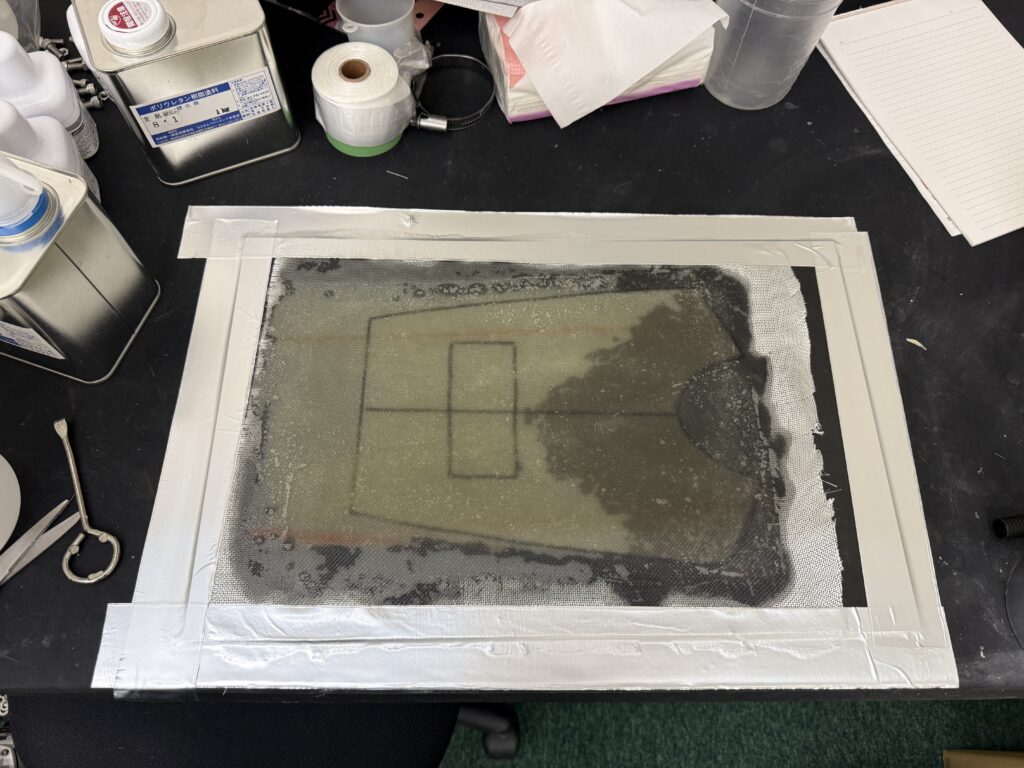
硬化が始まる前に、アルミテープで四辺をガッチリとテーブルに固定します。
これをPP板にせずに、鉄とかアルミなどの金属にしておくと絶対に反らない板が出来るのですが、生憎そういった材料が今回ガレージに見当たりません。
一先ずこうすることで、熱による歪みを最小限に抑えます(それでも僅かに反る)。
まだまだ続きます。