FRP型取り①
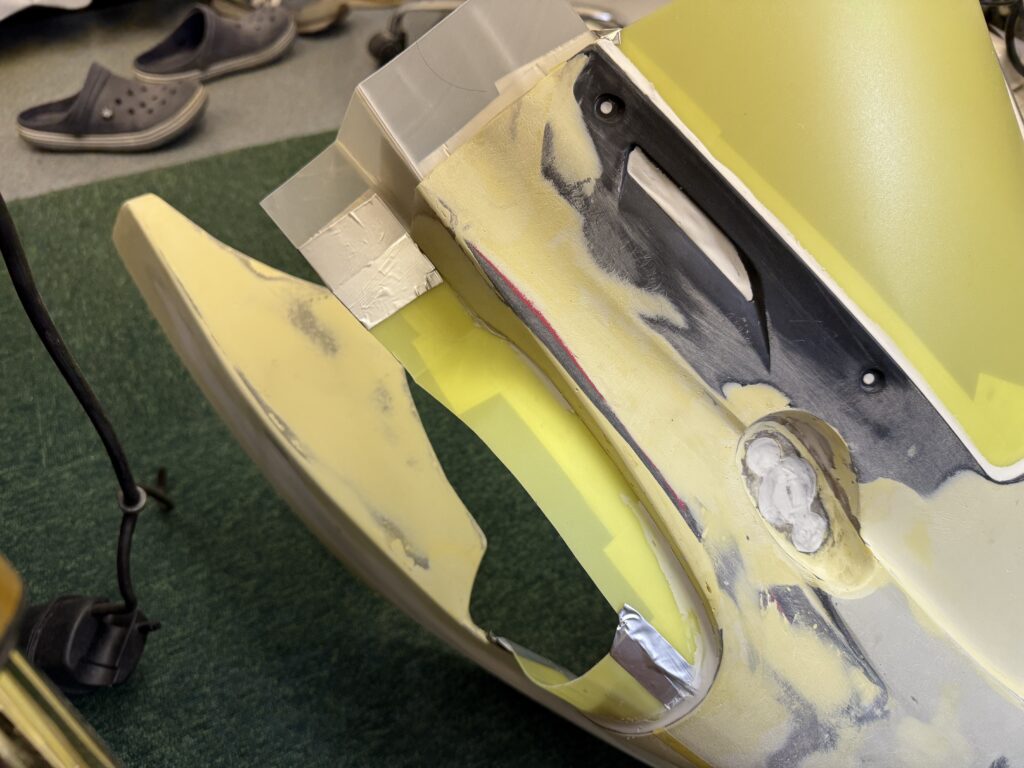
アッパーカウルの造形もバッチリ決まりましたので、いよいよ型取りを始めます。
まず型取りには油粘土が結構必要です(紙粘土ではなくあぶらねんどです)。
そもそも型と言うものは、硬いゲルコートとFRPで作る訳ですが、原型から型取りする際に、ゲルと原型が抱き着いて(くっ付いて離れない事)しまわぬ様、隙間という隙間にねんどを詰め込まなくてはいけません。
油粘土は熱にとても弱いので、使い終わったらあとの掃除のときに、風呂場で熱いシャワーと共に洗い流せるのも魅力の一つです。

次に注意する点は、このアッパーカウルの様に、立体的で複雑な物の型を取る場合は、不安定で動いてしまいそうな部位を無くすと言う事です。
このようにスクリーン部などにPP板などでブリッジして、固定しておく必要があります。
PP板をヒートガンなどで温めながら、上手く曲げることでテンションが掛からずに、楽に固定できるようになります。
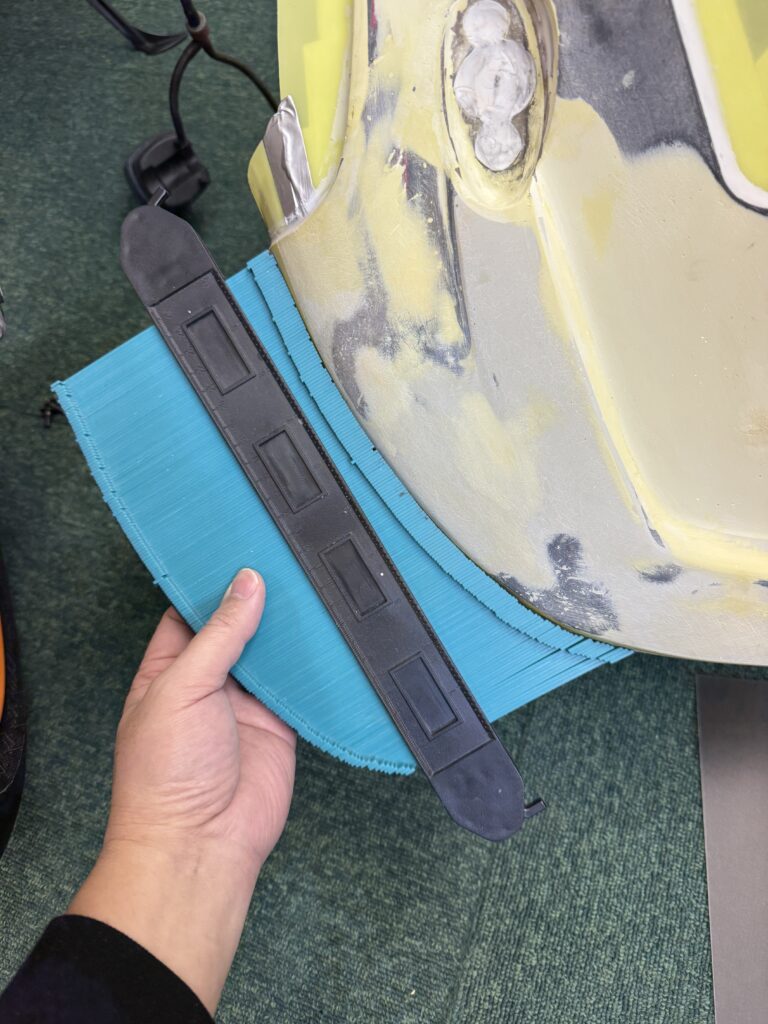
複雑な立体物の型を作るには、その原型の周囲にもリブを立てる必要があります。
これは、脱型時にタガネを打ち込んで抉る為の、始点や目印になってくれたり、割り型同士の境界線になることで、テコの原理が効くようになるためです。
又、リブを立てずに原型に全体にゲルを塗布した場合、ゲルが原型の裏に回り込んでしまう事でガッチリと掴んで離さなくなってしまい、型を破壊しないといけなくなってしまうのを防ぐ意味もあります。
車のボンネット複製の様に、表と裏を作って張り合わせる場合も、リブに窪みを所々に作っておくことで「位置合わせ機能」を持たせることも出来、とても便利です。
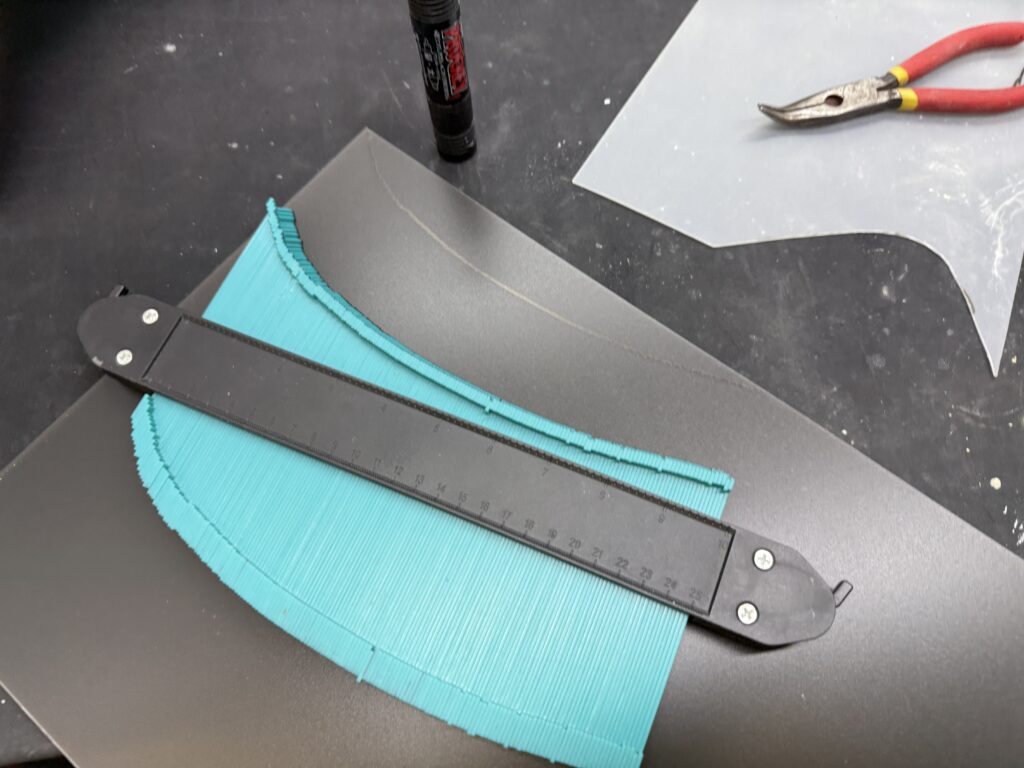
型作成に超重要なリブを作る為に、製品にピタリと沿わせたものを作る必要がありますが、それにはこのコンターゲージを活用します。
このコンターゲージを割り型の境界線に当てることで、PP板に正確にカーブを写し取ってゆきます。
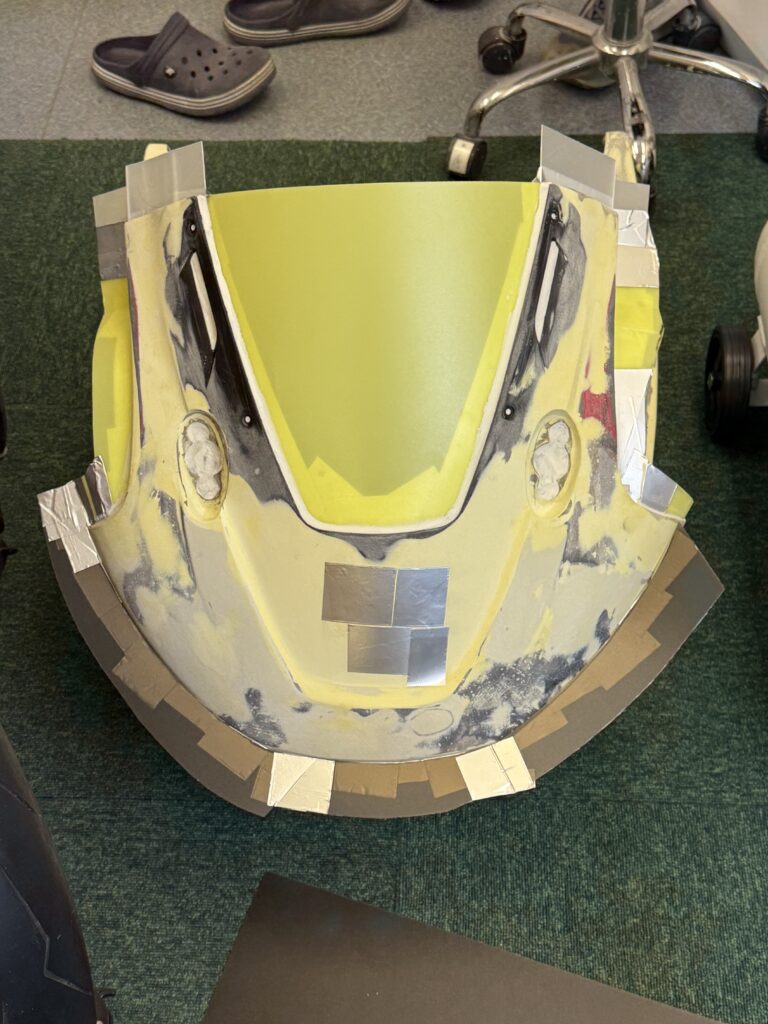
時間を掛け根気強くリブを立てて、製品各部に密着させたところです。
どうしても隙間が出来てしまった部分にはねんどを細くよじって押し込んでいます。
不安定な所は、表からも裏からも強粘着のアルミテープで固定してゆきます。
とにかくゲルには、壁の向こう側へ行かない様に、徹底的に隙間を埋めてブロックです。
そうしないと、すべての作業がリセットされてしまう「抱き付き」と言う悲劇が起こります。
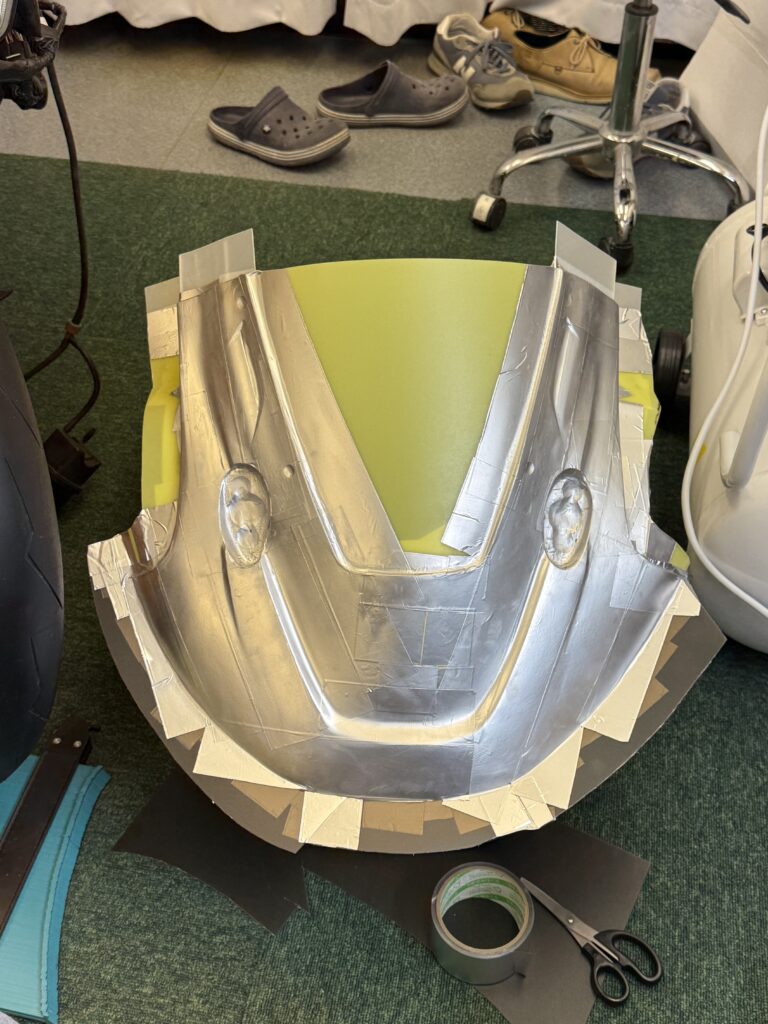
小物の型作成の前処理は、脱型のしやすさや施工性の面でもこのアルミテープ張りが一番です。
ボンリースと言うワックスを塗布してから乾燥させ、ブルーと呼ばれる離型剤を何度も塗布・乾燥させて脱型と言うのがセオリーですが、商売でも始めるならばいざ知らず、ただの趣味です。
精度が低くてもさっさと終わった方がハッピーであり、そんなプロやる工程は、修行したいなんて人じゃない限りやる必要はありません。
ネットにUPされている無責任で中途半端な情報を元に、正直に一通り実行し、失敗と成功を数限りなく繰り返した私の20年の経験からこう断言します。
素人はみんな、このアルミテープで脱型したらいいと思います。
テープのしわだらけの型が出来上がったって、形は大まかには再現されますから問題ありません。
結局は、塗装前に足付けしたり、サフを吹いたり、パテ埋めするんですから同じことです。
よくよく考えれば、手間を掛けられるのが素人の強みなんですから、楽しみましょう。
型が頑丈で超精密で綺麗である必要があるのは、業者さんがたくさん量産したいからです。
たった一個しか作らない素人が、プロ工程を守る必要なんてどこにもありません。
何でもかんでも”プロと同じようにやる事だけが正解”ではないと私は思います。
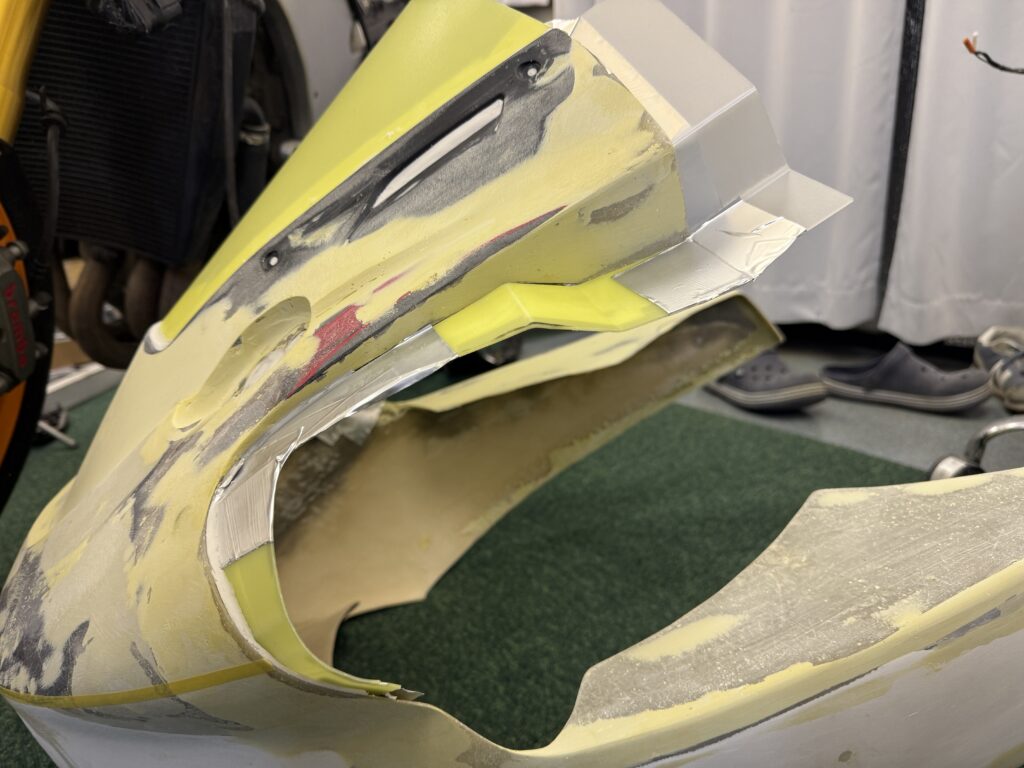
とにかく根を詰めずに楽しく出来ることが一番だと齢52となり思う訳です。
それが長く趣味を楽しむコツなのかなと。
いまどきネットには様々な”警察”さんが居ます。
FRP警察、塗装警察、デザイン警察(笑)。
”決めつけデカ”の言う事に一喜一憂せず、みんな好きに楽しめばいいと思う今日この頃です。
バイクなんて髪型や洋服のような物。
本人がそれでいいと思ってりゃ、いいんです。
FRP型取り②
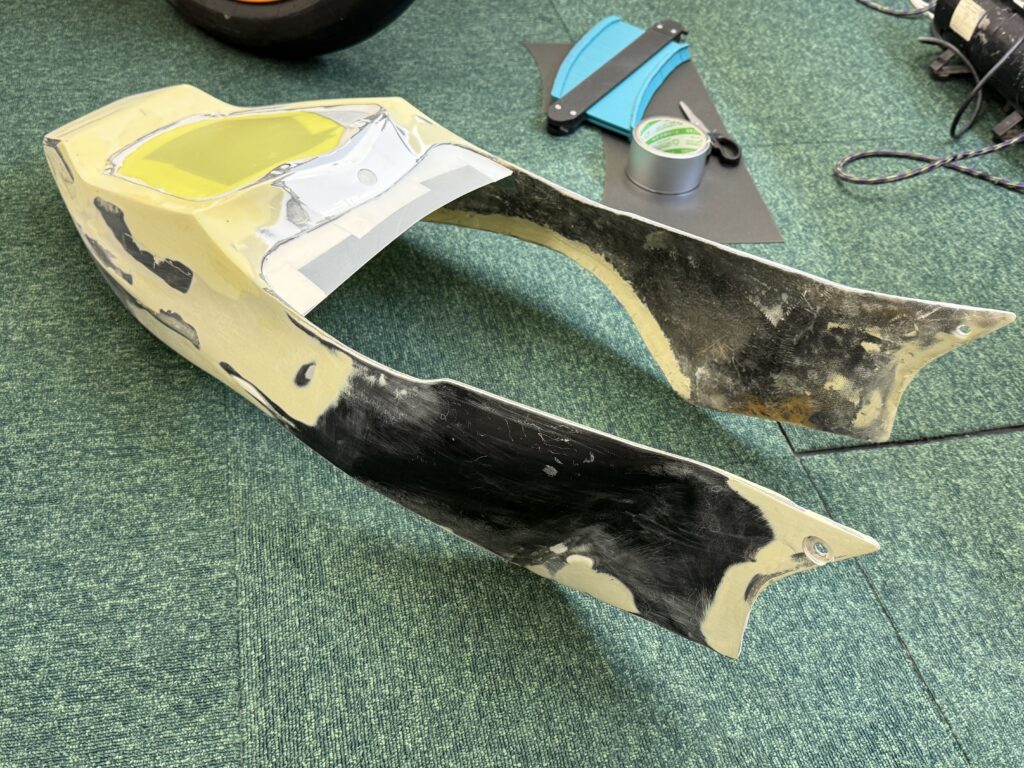
シートの型作成にも着手します。
このシートの難しいところは、大型であることに加え、前方が解放されているので、カウル自体が”動いてしまうこと”にあります。
ここに注意しないと、後々おかしなことになってしまいます。
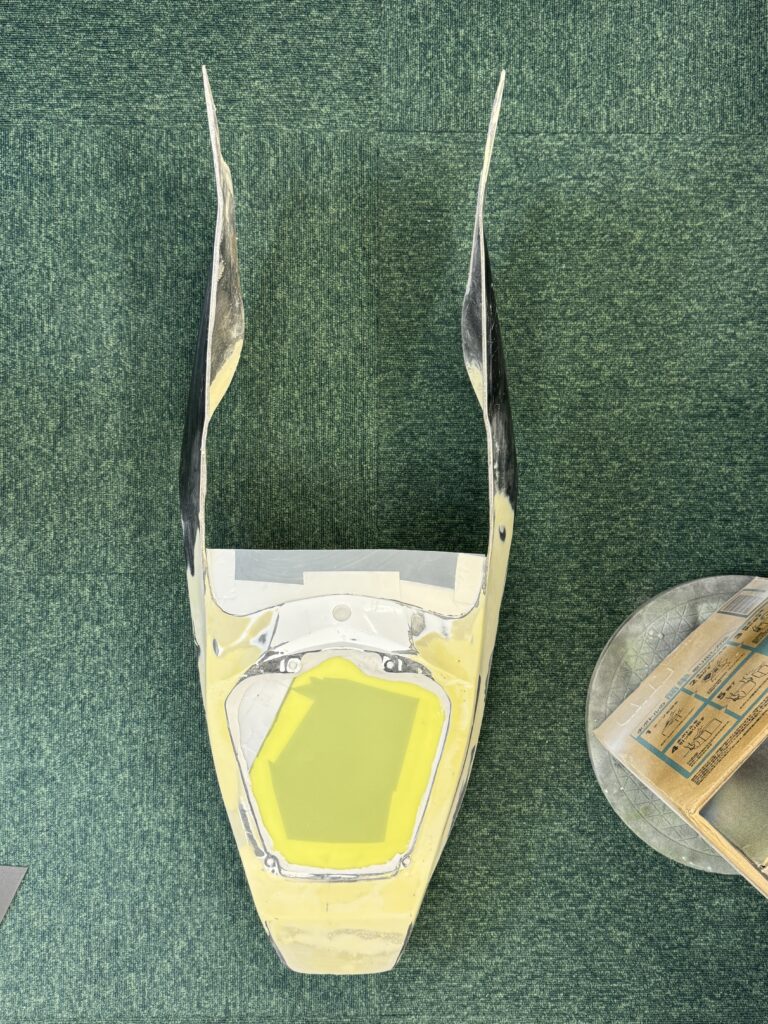
小物入れ部分も同じことが言えます。
ここをしっかりと塞いで固定しないと、シートカウルに左右の歪みが出ます。
PP板を形通りに切り出したら、表と裏からアルミテープでガッチリ固定して、隙間という隙間をしっかりと粘土で埋めてゆきます。
鍵穴などは位置が分かるように、一度裏から蓋をしてから粘土で埋めたら、今度は上からアルミテープを貼って少し指で押し、凹ませておきます。
そうすると、穴の周辺だけ綺麗に窪んでくれるので、脱型後の穴あけに悩むことが無くなります。
純正カウルの正確な穴位置は助かるので、小物入れの四方のビス穴も同様にします。
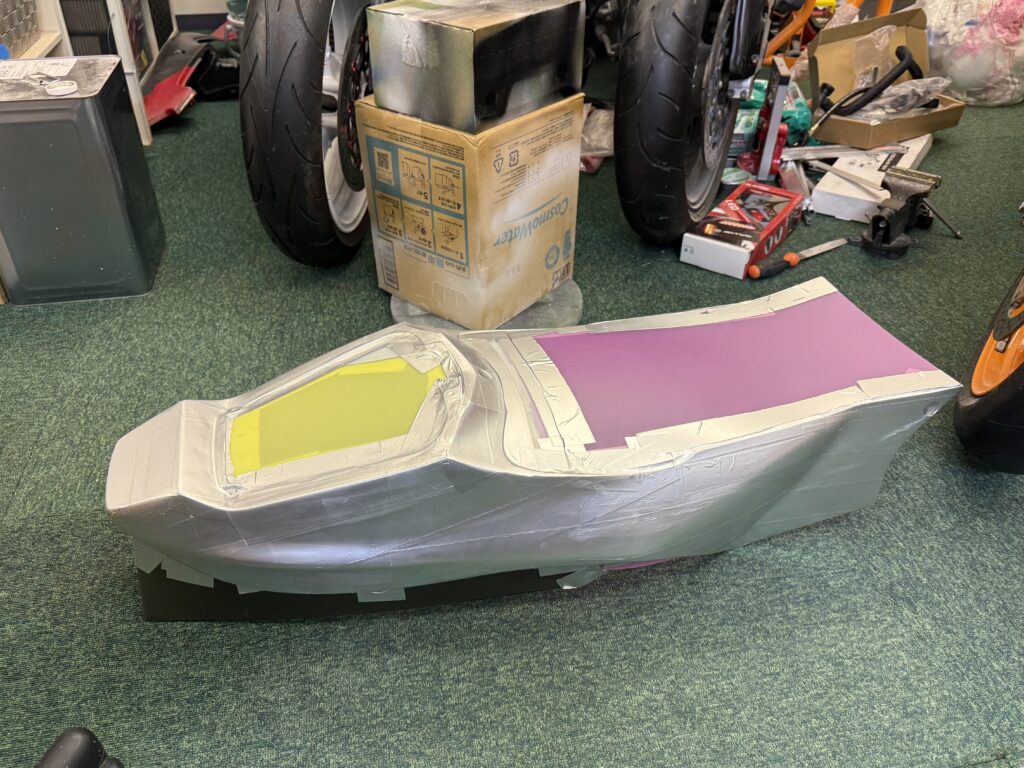
各部をしっかりと計測してPP板を切り出し、残りの部分を埋めました。
アルミテープを全周に渡って貼り込み、脱型に備えます。
PP板はもともとFRP樹脂が食わずに離型する為、テープを貼らずともOKです。
※テールランプはカウルと面一か、少し飛び出していた方が車検を受けるうえで無難との指摘があったので、この後形状を変更します。
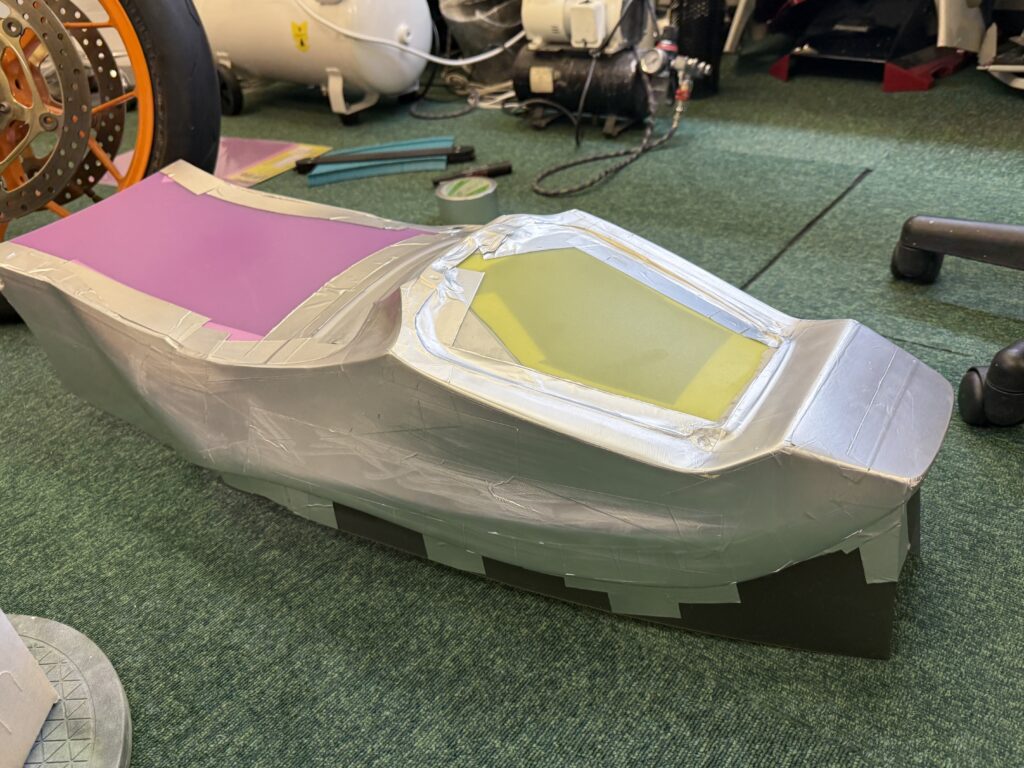
尚、大型製品の築層には少し注意が必要です。
大型になって重量も増すので、樹脂を含んだFRPの自重に耐え切れず、剥離することがあります。
又、作業者の作業性も悪くなるので、検討する必要があります。
必要に応じて「足」などを作ることによってこのように自立出来、作業がはかどる事があります。
足があると、脱型時に力を入れやすくなり、これまた作業性が上がります。
この後、真ん中に仕切り板を作ってしまえば、型作成準備は完了です。
そうそう。
勘のいい人はもう気が付いたと思いますが・・・・今回はオリジナルカウル作成に関して書いていますが、実はこれ、既存のカウル複製にも共通して使えるテクニックなんです。
難しそうなカウルの複製も、こんな風に個人で出来ない事もないんですよ。
さて、重整備ならぬ重カスタムはまだまだ続きます。