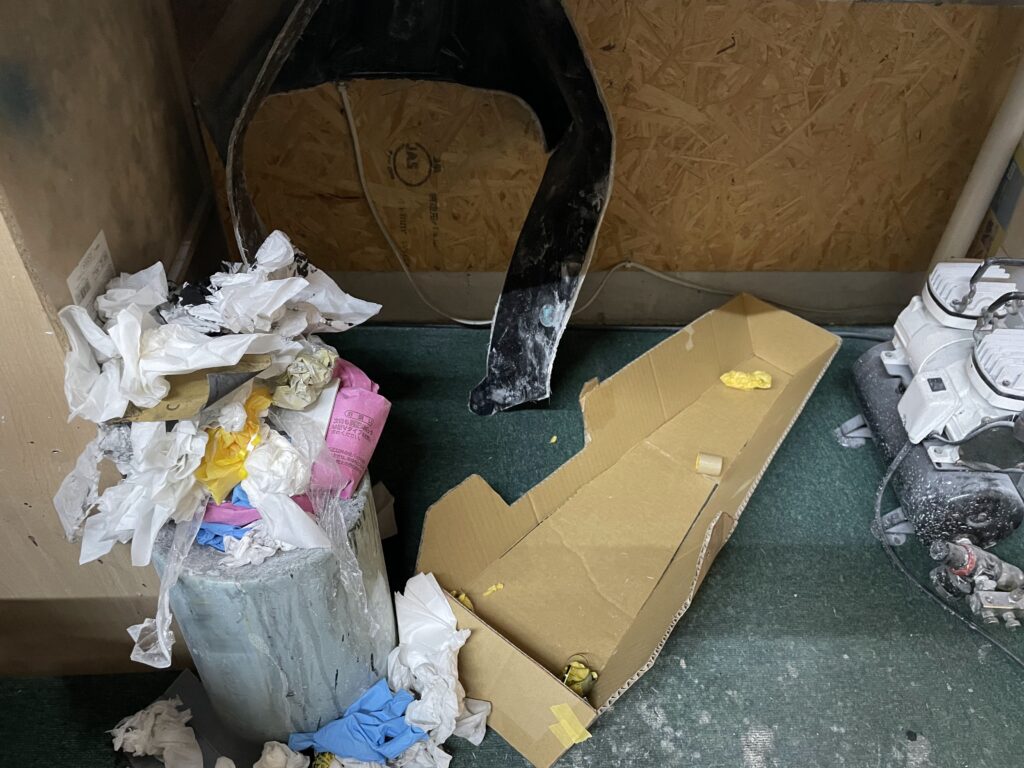
理想と現実の間
理想と現実は学校でも会社でも、子供にも大人にもある訳ですが、ワンオフカスタムにもあります。
いつもカッコよいCG➡出来ました!的な写真で、見ている方はさぞや”高まる”訳ですが、そこに至るには並々ならぬ苦悩があり、苦痛を伴う作業の連続です(笑)。
先に言っておくと今回は、面白くありませんよ。
なのですっ飛ばしてくれて構いません。いやほんと。
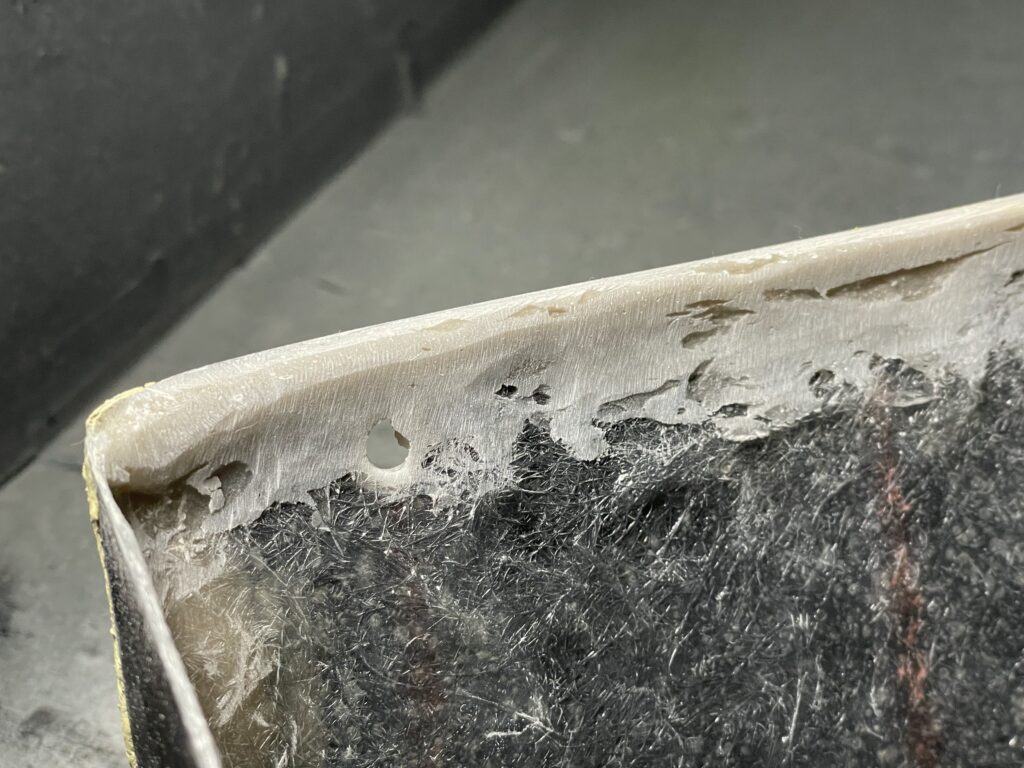
カウルには様々な力が掛かるので、それに対抗するにはFRPマットの築層枚数(プライ数)を増やして対応するのですが、そうすればそうするほどに、硬く・重たくなります。
それらを回避するために、なるべく薄く・軽く作りつつもギリギリの強度は欲しいのですが、これを実現するには「折り返し」を作るのが最も定番です。
しかしこの「折り返し」は型を作成する上で、抜けなくなる原因ワーストワンであり、90度直角に短く折り返すもんだから、FRPマットは樹脂に含侵してても、そう簡単には曲がってはくれません。
そこで今回チャレンジしたのは”リブを立てる”と言う作業です。
平面の歪みを押さえる事も出来る「ミゾ」であることの多い”リブ”ですが、今回はエッジの部分のモールとして、折り返しの代わりに作っています。
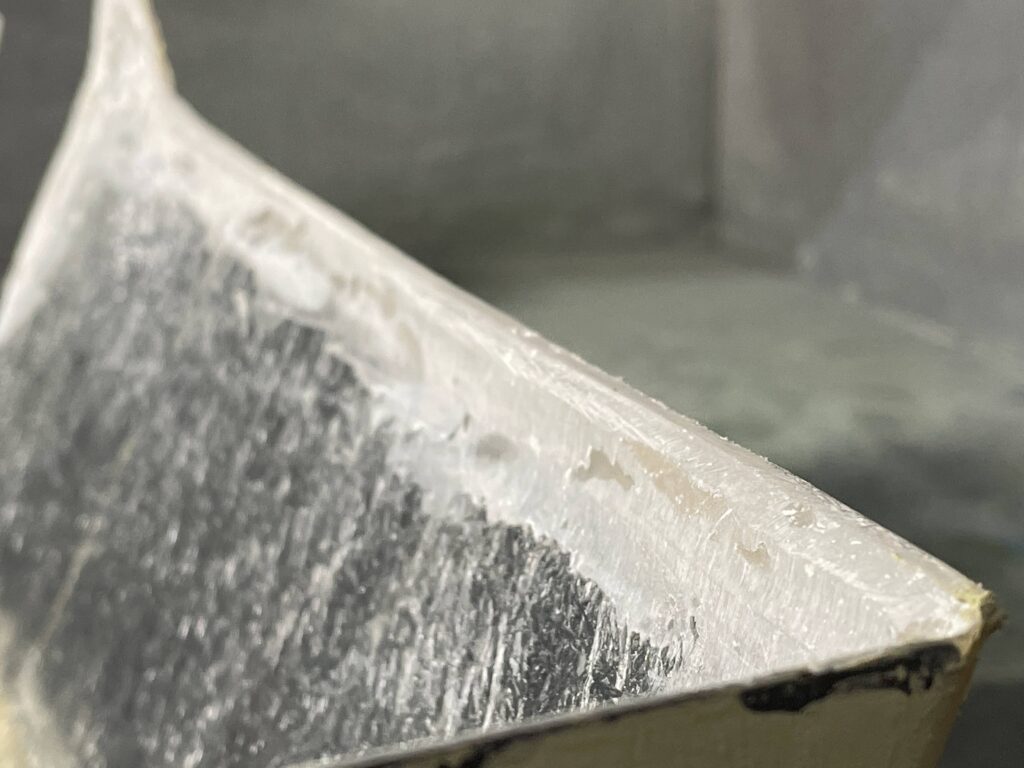
まず、タルクにFRPマットをチョップした物を混ぜ、それをパラフィン入りの樹脂で練り込んだ”簡易FRPパテ”を自作します。
硬化する前に素早くヘラに適量取りながら、カウルの淵に沿って内側にしごく様に載せて行きます。
硬化後はベルトサンダー等でバリを取る様にサッとサンディングして仕上げます。
純正のABS樹脂製のカウリングなどは、よく淵の部分が「もりっと」なっています。
純正カウルは、あからさまな折り返しが無い(アッパーカウルのナックル部分とかね)のに、どこを掴んでも、ある程度の形状を保てる秘密は、このリブが強度を保証しているからなんです。
今回はこれを後付けで再現することで軽いまま強度を保つことに成功しました。
面出し沼
何にでも”沼”の様にズブズブとハマってしまう世界が存在します。
このパテを使った面出し作業も、そういった底なし沼の一種だと言わざるを得ません。
今回は丁度いい(いや・・・良くない)ので、このアンダーカウルで見てゆきます。
このように長く、道路の様に平滑な面がずっと続く部品は、実はそう簡単に作る事は出来ません。
サイズ感を出すための段ボールから型を取り、PP板を何枚も切り出して両面テープで止めて強度を確保し、なるべく歪みの無い平面を作ってから型起こしをしても、FRP樹脂は発熱しながら収縮して硬化するので、硬化の過程で100%何らかの歪みが生じます。
完璧な型が存在し、一層ずつノンパラで時間硬化の間隔をおき、更に低収縮樹脂を使って、少ない硬化剤で仕上げれば、何とかイッパツOKとなるかもしれませんが、そんなことをやっている設備も時間もありません。
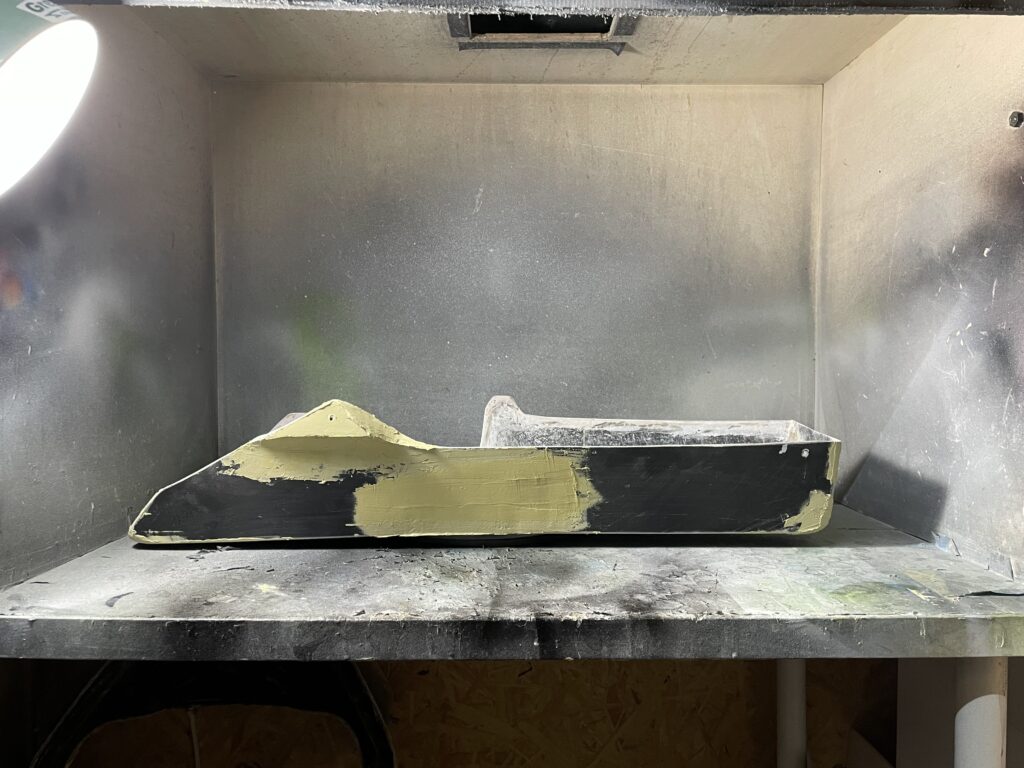
結局チャチャっとやって、後からパテで面出しした方が早い訳ですが、この面出し・・・やり方によってはいつまでたっても終わらないループにハマることになります。
これは、あえてやってみた悪い例の写真です。
4cmくらいのプラスチックの安い100均のヘラで、照明の明かりを頼りに隆起を確認した上で、必要なところにパテを載せましたが、結局ヘラの全幅がカバーしたい面積よりも小さいので一回のしごきでカバーできず、何度も何度も補修面を往復するうちに、厚く塗りすぎたパテが動いてしまい”波打った面”が出来ています。
ここで「まあ、あとで削ればいいさ」と高をくくってはいけません。
この状態で硬化した後に削っても「滑らかだけど僅かにデコボコな面」が完成し、それをカバーしようとまたパテを盛る・・・・と言う永遠のループに突入してしまうという訳です。
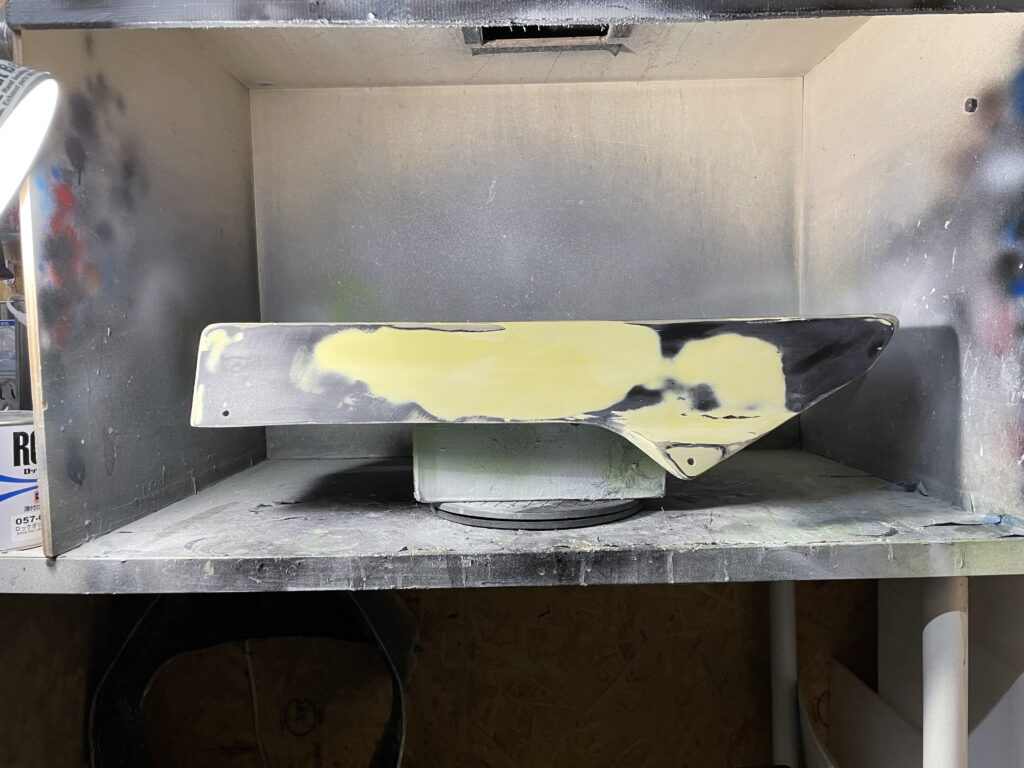
これを回避するには、パテナイフを使います。
幅広で金属製の動かないヘラで、ある程度の量のパテを取り均一な力でサッとしごいてゆきます。
目で見ても分からないレベルまで凹んでいるところにパテが必要なだけ入って行き、硬化後も殆どサンディングの必要が無い程の、平滑な面が一気に出来上がるのは面白いです。
パテを厚盛りしすぎると、硬化してシンナーの成分が飛んだ際にパテが少し痩せることがあります(引け)が、気を付ければ大丈夫です。
硬化後は、大き目のサンディングブロックを使い、局所的に力が掛からぬように均一に優しく水砥ぎすれば、美しい真っ直ぐな面を一発で出すことが可能です。
道具はどちらも大した値段ではありませんが、あると無いとでは雲泥の違いですので、チャレンジする人はぜひ揃えておきましょう。
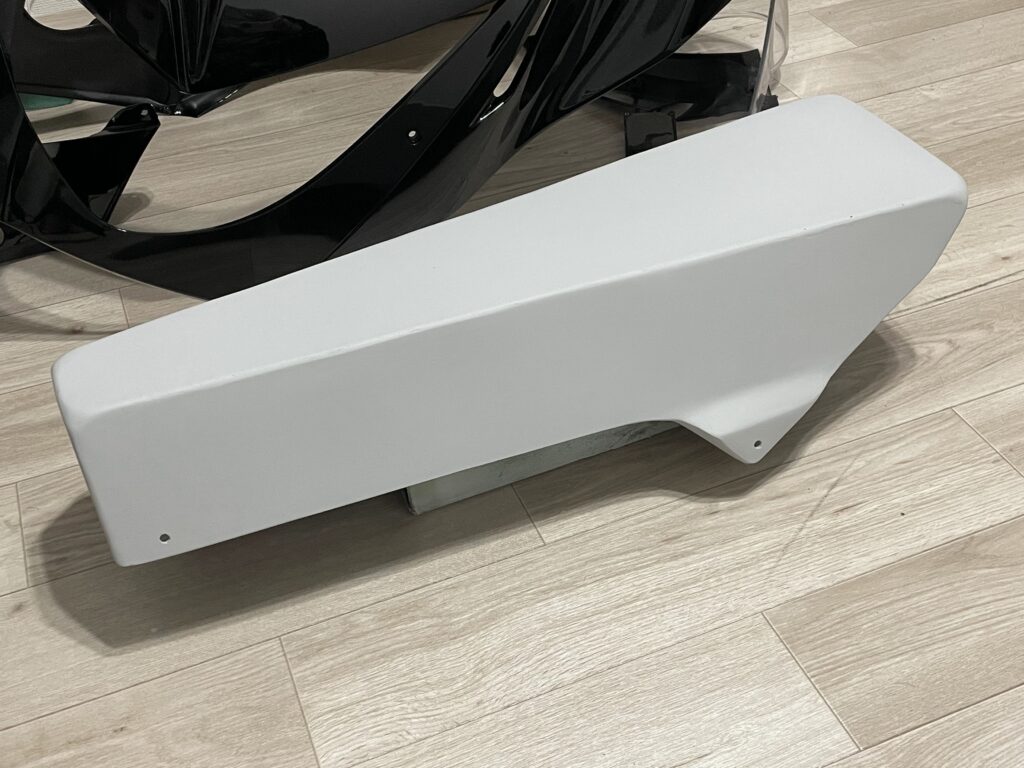
幾つもの失敗を繰り返し、たどり着いたのがこの姿です。
パテを水砥ぎしたのち、シリコンオフでしっかり脱脂してから、プライマーを吹いた状態です。
金型も無しに、手作業でゼロからここまでのクオリティの物が作れます。
マスターモデルは型の原型なので、この型に不具合があれば、その不具合も一緒にコピーされます。
どこまでやっても終わりはありませんが、10人中9人が「素晴らしい」「すごい」と言ってくれるようになるまで、この細かい作業は続いてゆきます。
急がば回れ
急がば回れとはよく言ったもんで、これはカウル塗装にもピッタリです。
先に書いたパテに残った水砥ぎの際の水分や、プライマーに含まれるシンナー成分などが残っている状態のまま上から塗装をすると、硬化していたはずの層が元に戻ってしまい、しばらくたつと火傷のように膨らんできてしまう事があります(膨れと呼ぶ)。
パテをしっかりと時間を掛けて乾燥させ、余計な成分を飛ばすことが大切です。
今回使う白は、青っぽい白物家電のような白が下塗りになっていますが、すこぶる隠ぺい率が悪く下地のパテの跡などがいつまでも透けて見えています。
ドライ吹きを行わず、バサっと塗ったら垂れてしまいました。
白は、LEDライトなどの強い照明器具が無いと、どのくらいウェットに塗料が乗っかっているのか判別が出来ず、塗装の難しい部類に入る色です。
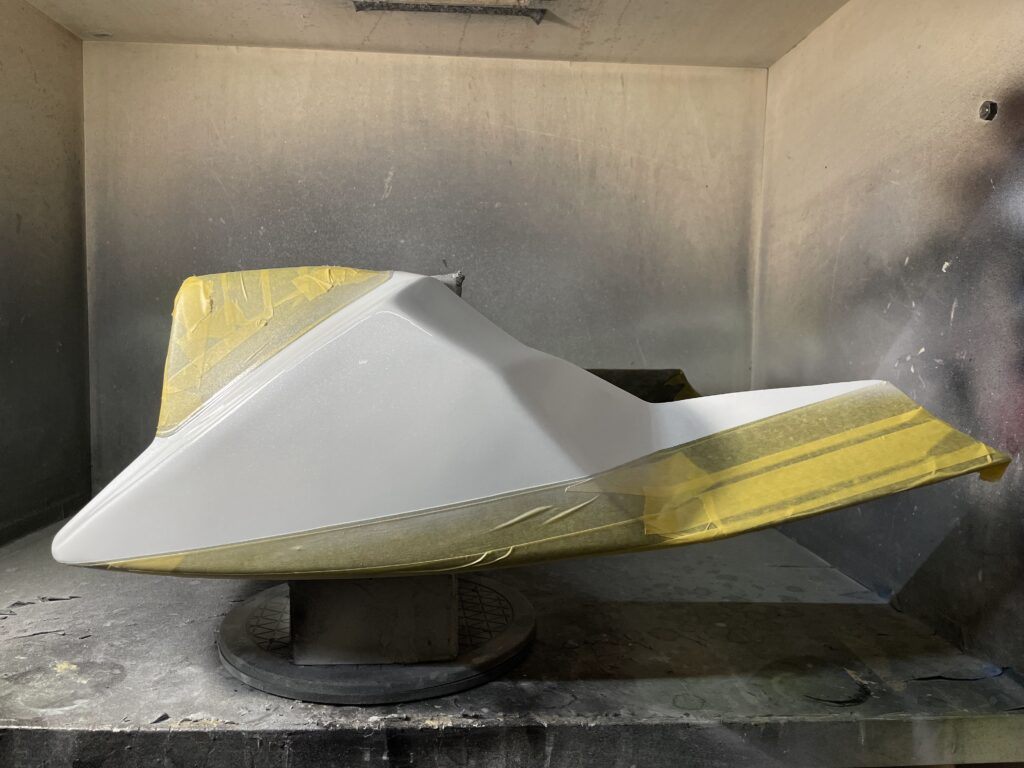
しっかりとマスキングしてから、3回ぐらいに分けてパラパラとドライ吹きした事でザラザラした塗装面=足場が出来ます。
こうすることで、塗装面に対し、塗料が踏ん張る(とどまる)為の粘り気のある足場が出来上がるので、簡単には垂れなくなります。
その後で、艶が出るようになるまでウェット吹きします。
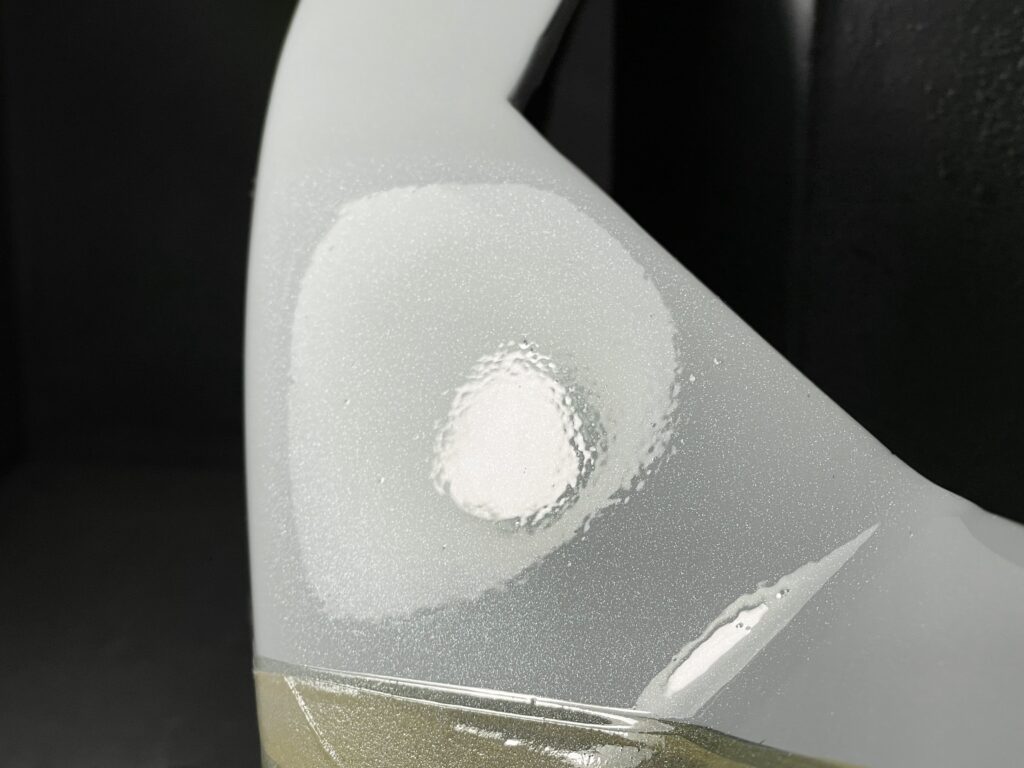
しかし、ザラザラの足場の上にウェット吹きした直後は、このように「柚子肌」になります。
せっかくツルツルになるまで砥いだ面が、塗装によってまた凸凹になったようでがっかりしてしまいますが、面白いもので、塗料に混ぜている伸びの良いシンナーは、この後ザラザラの足場と溶かしながらまじりあって、時間と共にツルっとした面に変化してゆきます。
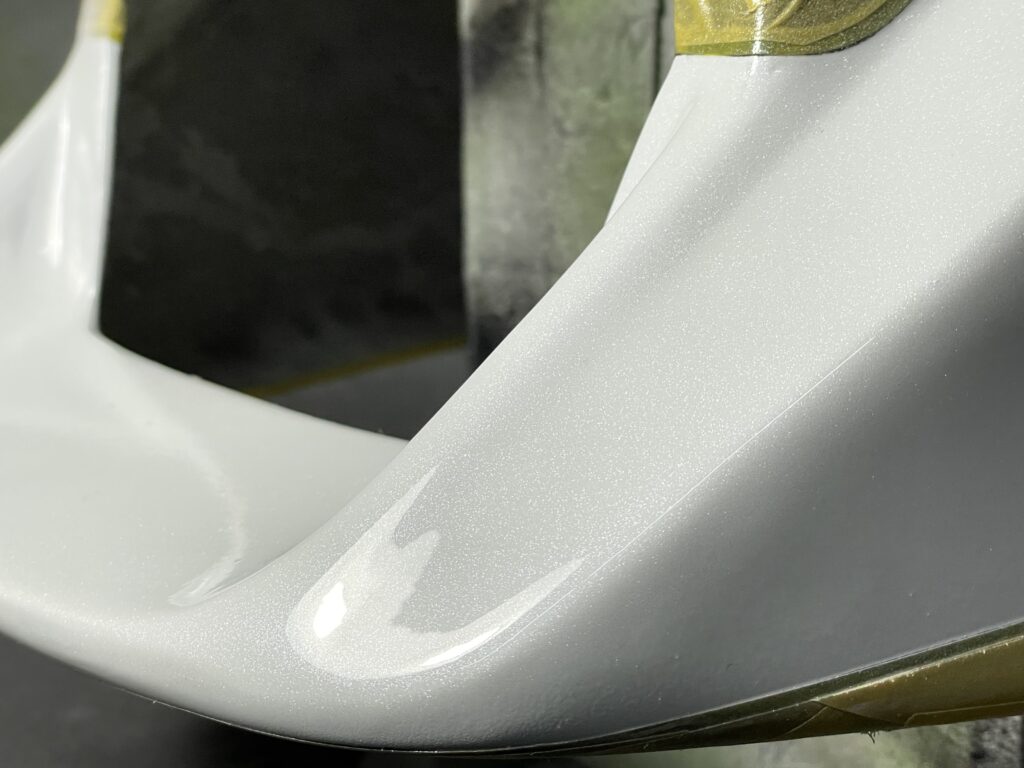
それゆえ、塗装面が柚子肌になったことに焦ってしまい、乾いていないのにムキになって更に塗料を吹き付けるのはご法度です。
そんなことをすると、1000%塗装が垂れて大失敗です(笑)。
この場合の正解はなんと「待つ」こと。
先にドライ吹きした半乾きの塗料の粒は、後からドバっと塗られた塗料につつまれて、もう一度緩くなり互いに溶け合います。
我慢して待っていると、塗料は溶けあいつつ乾き、このように綺麗な塗膜が出来上がります。
少しずつ時間を置きながら、塗り重ねを進めることこそが、結局は確実で完璧な塗装になるのです。
尚、このマスキングを「剥がすタイミング」も実は難しいのですが、私の場合マスキング部分にわざとはみ出して少し吹いておき、15分くらいのインターバルの後、指触乾燥が出来ていることが確認できたた時に剥がすタイミングとしています。
これは遅くても早くてもダメで、遅いと塗料が繋がったまま硬くなり、見切りを超えてペリペリと塗った部分まで剥がれます。
逆に速すぎると、粘り気のある塗料が糸を引いてしまい、ほかの塗装面にペタっと付着してしまいます。
そして、実際に剥がす際は、対象に対して90度ではなく160度くらいの角度で「塗装面の境界線を切る」様に剥がすと綺麗に見切れます。
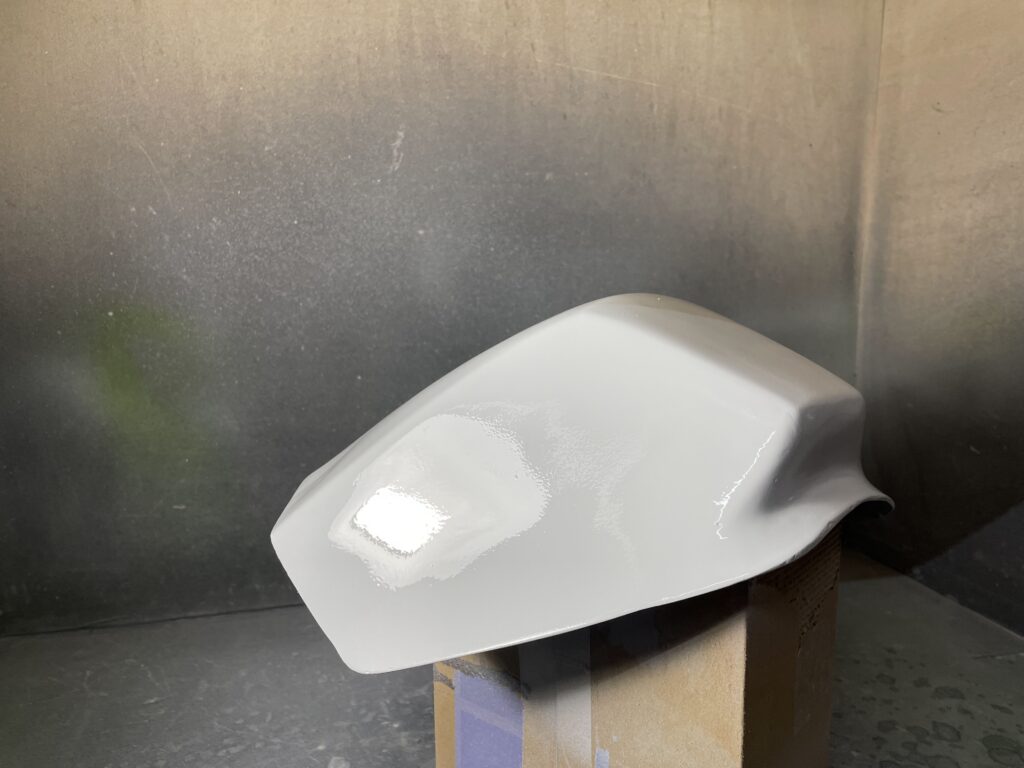
塗料によっては、下塗りにソリッド色があり、その上塗りに薄いパール系の色を載せる事で、初めて完成する色もあります。
2コートパールと言うものは、上塗りの重ね加減で色を調整できるわけですが、逆に言うと再現性にばらつきが出来るとも言えます。
今回は下塗りの白の上に青っぽいパールが薄く乗りますが、下塗りが白な為にどのくらいパール塗料が乗っかっているかが全く分かりません。
故にパールもパラパラとドライ吹きを重ね、最後におっかなびっくりウェットに塗ってます。
塗装作業とは、傍目には一瞬で終わってしまいますが、様々な知識と段取りが必要で、それらを季節(気温や湿度)に対して、自在に変更すると言う判断ができないといけない、奥の深い世界なのです。