折り返しを作る②
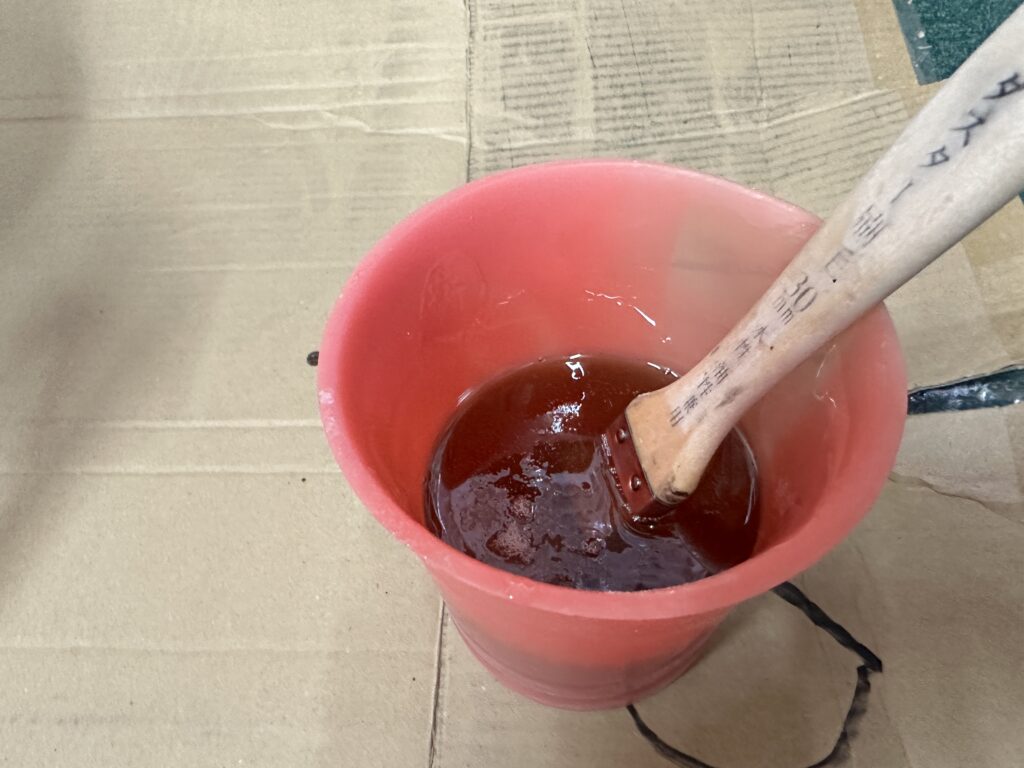
はい、この回はツマンナイですよーと先に言っておきます。
この車両のオーナーになるつもりで見ている方か、同じような事をやってみたくてウズウズしている人向けであり、カスタムのHOW部分のみだから、全然華がありません(笑)。
良く、FRP成型の記事に「それどころじゃありませんでしたので」と書かれて写真がすっ飛ばされていることが多いのですが、全くその通りで、樹脂で手がベタベタになる為それどころではありません。
何かを触る度に被害が広がるそんな状態で、スマホで写真とか無理だし、一度樹脂に硬化剤を混ぜたら、遅かれ早かれ硬化が始まってしまいます。
しかし、寒い冬は樹脂の硬化スピードがとりわけ遅くなりがちなので、これを機に撮影してみようか?と思った次第です。
実は樹脂には「春夏秋冬」があるので、その時期に合った樹脂をタイムリーに少量買うべきです。
私のは秋に大量に買った樹脂ですので、冬にはちょっと厳しい様で、最初からドロンドロンです。
硬化には一定の温度も必要なので、ガレージを目張りしてからストーブをガンガンに炊きつつ、しっかり換気すると言う、なんとも不経済な状態でスタートします。
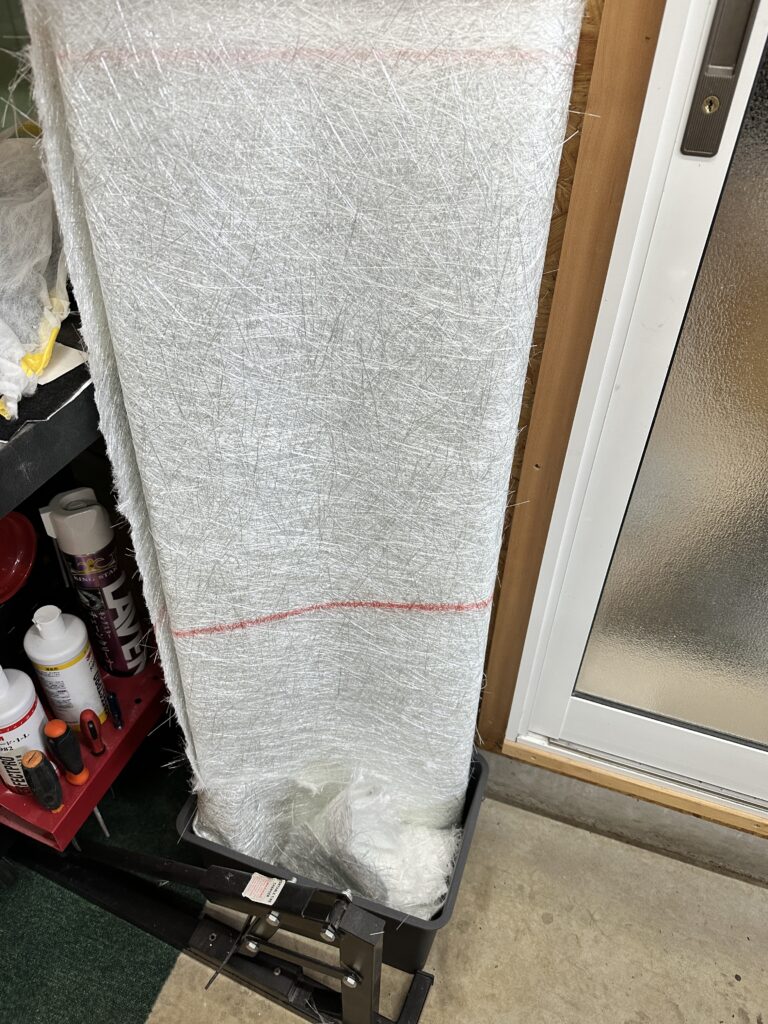
FRPカウルを作るには、FRPマット以外にも、実は数種類使います。
一つはこのチクチクの「マット」と呼ばれている物で#450~#380が普通です。
それ以外には、クロス(ツルツルの生地)やサーフェイス(ティッシュのよう)と呼ばれている物があります。
一番最初に型にゲルを塗布して、硬化後に一枚目のマットを貼り、芯材として二枚目にクロスをペタリ、丁寧にしたいのであれば、化粧でサーフェスマットを貼って完成です。
これで約2.2プライぐらいの最低強度のカウルが出来ますが、面積の大きいところだと、手で押すとベコンベコンで、何となくレース用って感じです。
ストリートならばマットをもう一枚多く二枚貼って、全部で3.2プライにしたいですね。
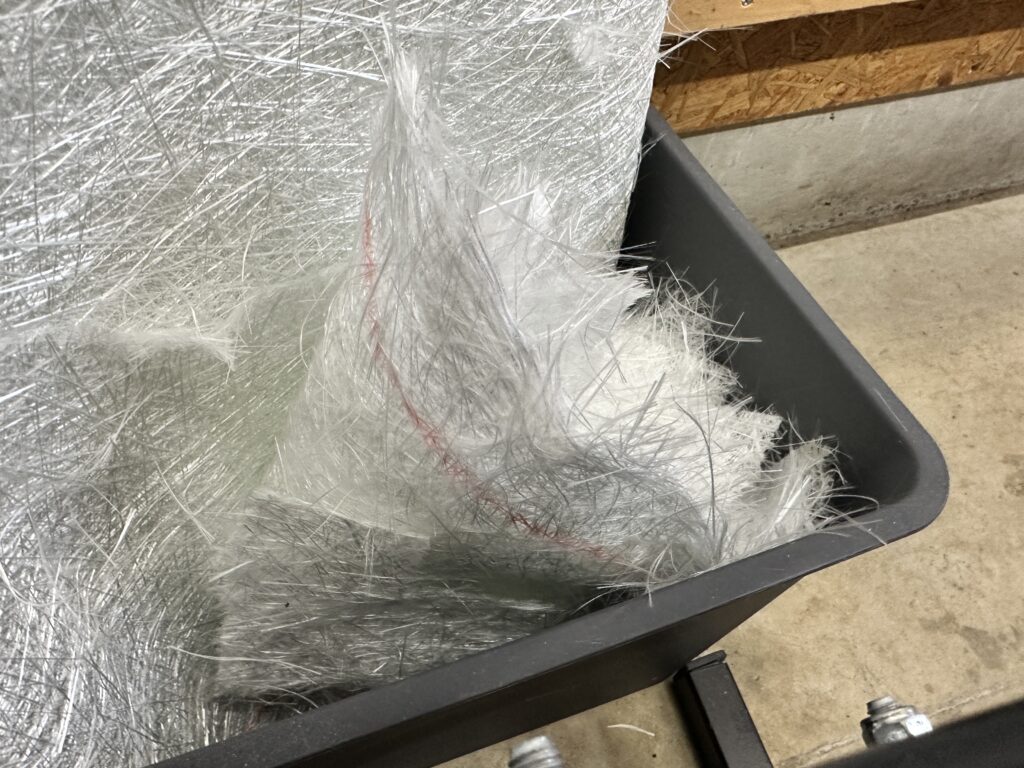
マットはチクチクのままだと上手く曲がってくれないので、事前にモミモミしておきましょう。
揉む際にはガラスの飛沫が飛散するので、しっかり換気しつつ防毒マスクは必須、手袋をしないと手や指がとんでもない事になります。
何とかしてクチャクチャにしておいたマットは、常に少しストックしておくようにすると、すぐに作業できて便利です。
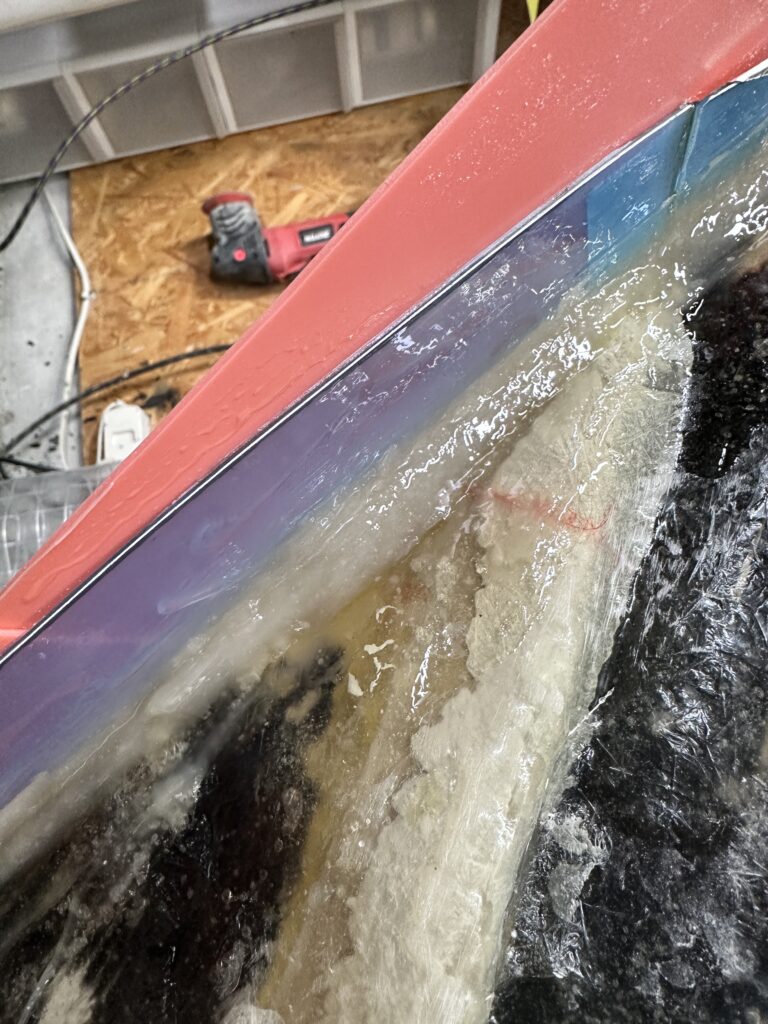
前回ファイバーパテを接着剤代わりにしてパネル同士をくっつけましたが、同時に90度直角の部分に対して詰め込んでおり、90度の直角を緩いRに変化させておきました。
これは、FRPマットを揉み込んでも、90度には曲がってくれないための対応なんです。
最初は樹脂のベタベタでマットが張り付いて見えても、硬化と共に徐々に反り返って離れて来てしまい、対象と空間が出来た状態で固まってしまう事で、完成後大きな巣穴が沢山出来てしまいます。
これを事前に防止するために、ファイバーパテを角に詰め込んで、直角を潰しておいたという訳です。
逆にこの方法なら、通常できないはずの「鋭角なFRPカウル」を作ることが可能です(その分、重くなります)。
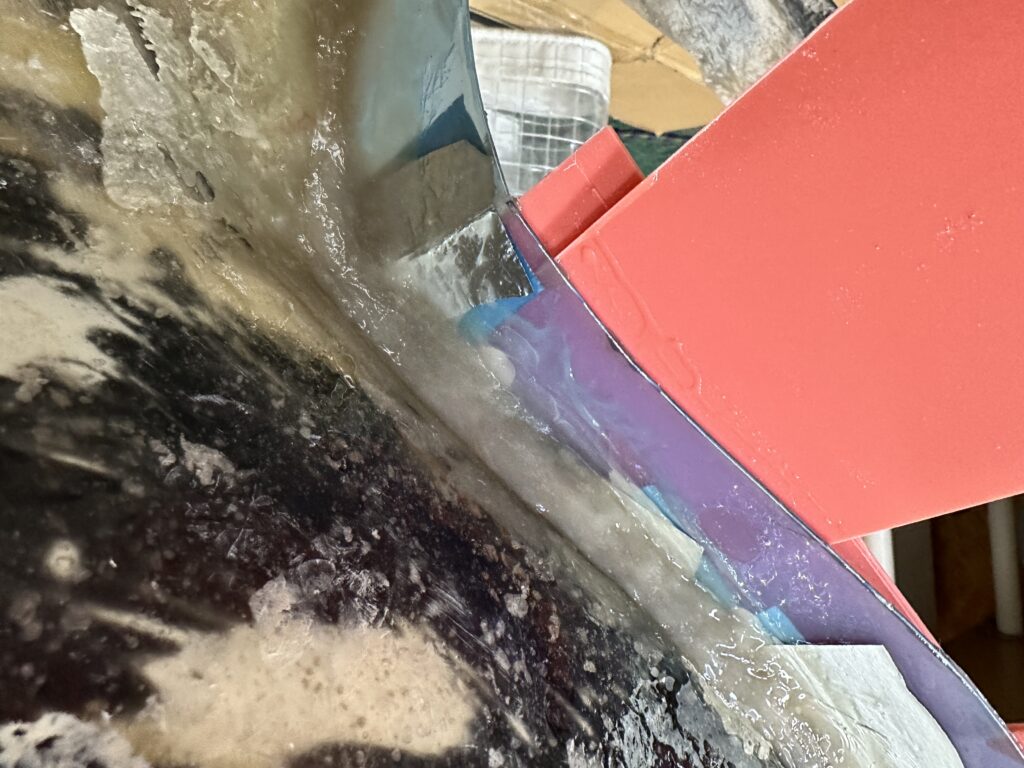
そんなこんなで、まんべんなく埋めまくっておきました。
私が作るカウルは、毎回エッジが効いていますし、今回だってそうです。
重くなるし(そんなにでは無いけど)、離型は悪いし、面倒くさいのですが、デザインは譲れません。
これは、採算や量産性を全く無視した、ワンオフだからこそ出来ることです。
そして、巷に溢れかえる量産品カウルが常にぼんやりとしたラインを描く理由でもあります。
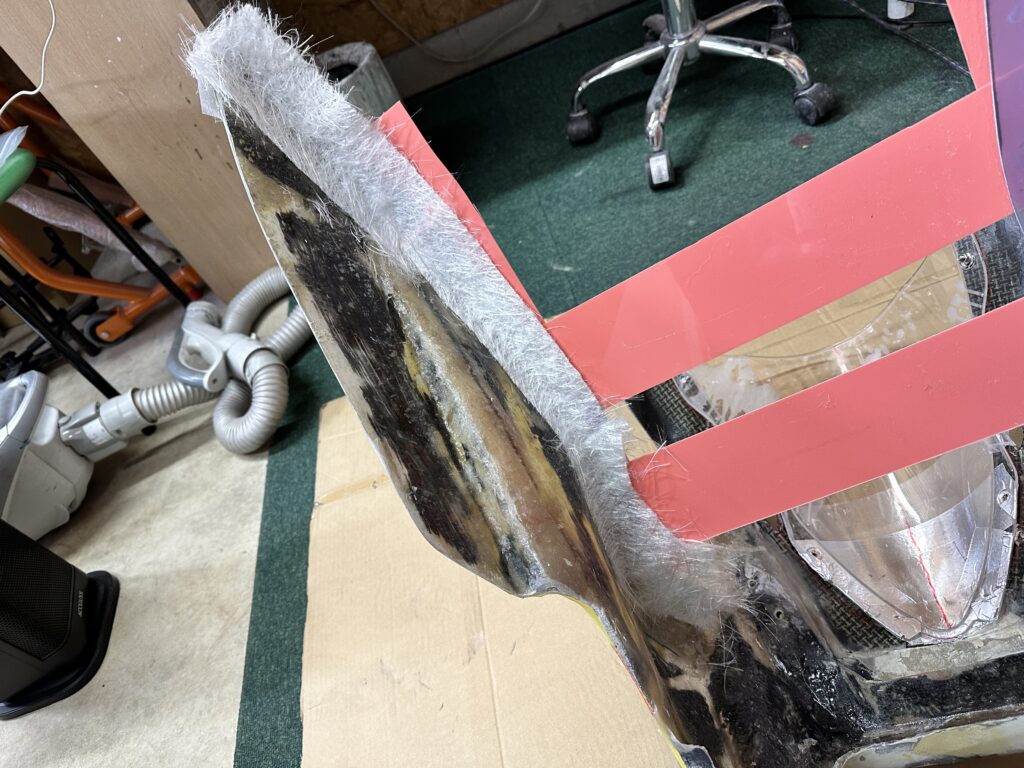
まずは接着剤代わりに、樹脂を刷毛で対象に塗り、少しだけ乾かします。
ノンパラなので、乾いてもベタベタの状態ですが、粘着性を最強にするためにちょっと待ちます。
最強になった頃合いを見て、あらかじめ用意していたマットをまずはチョコンと置いてゆきます。
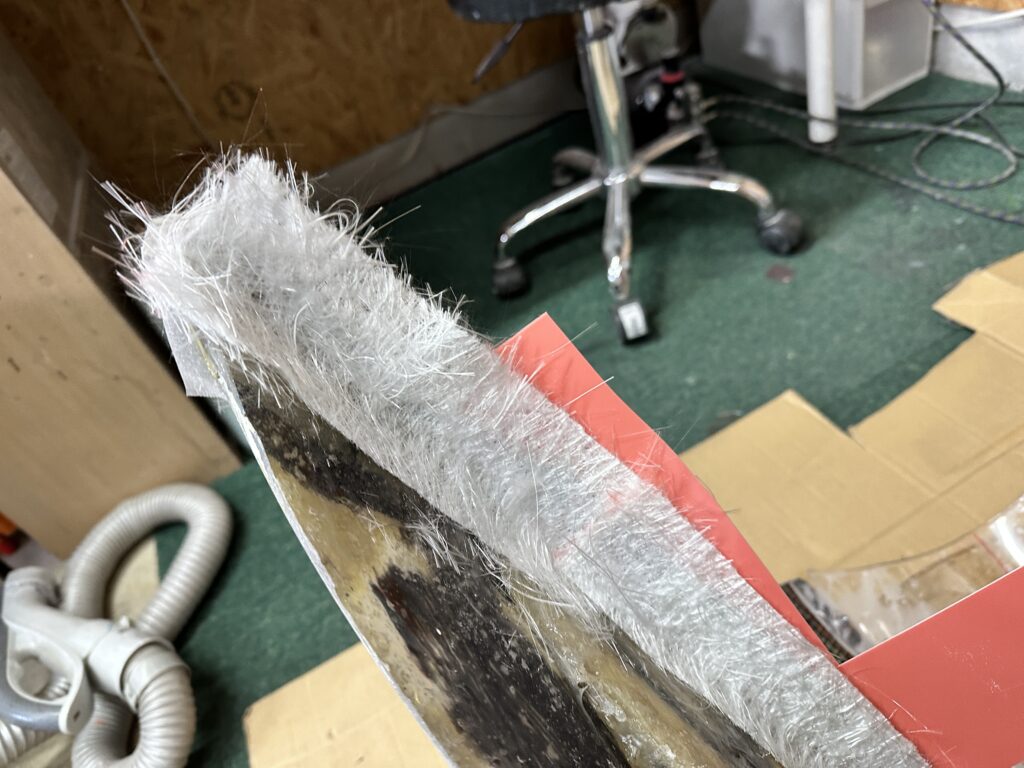
少しだけ角に掛かる様に指で押し付けながらチョンチョンと押し付けてゆきます。
作業には厄介なノンパラの粘着力が、糊の様に頼もしい瞬間です(笑)。
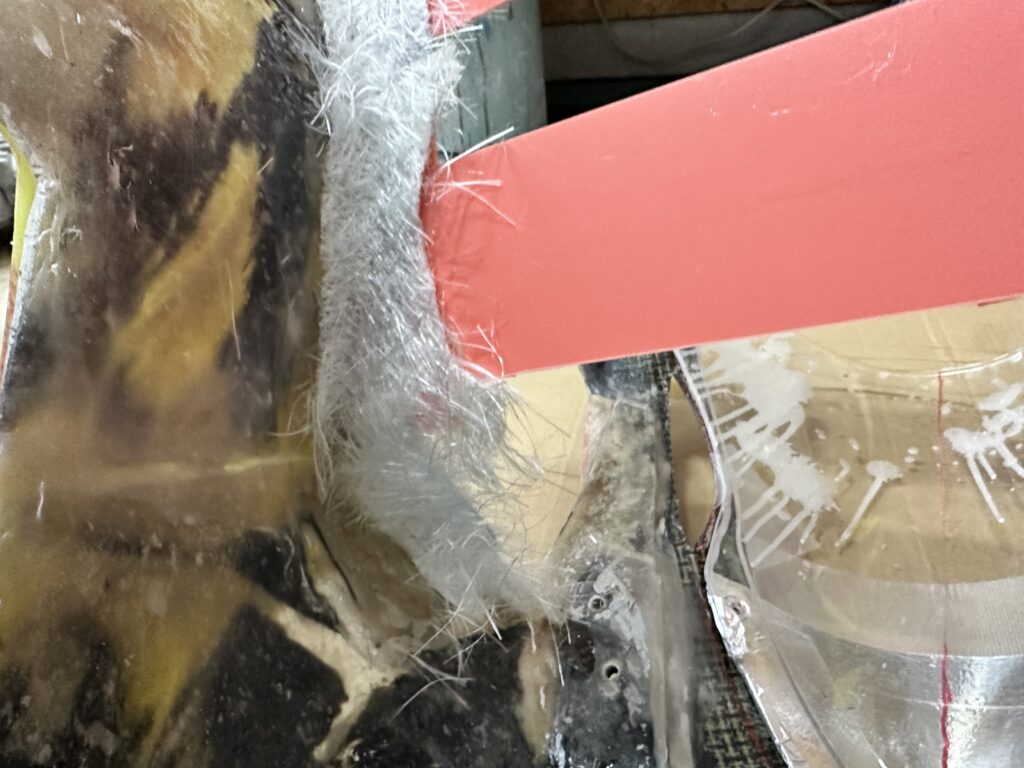
折り返しの角度が付いていたり、方向が変わる複雑な形状の部分などは、特にマットを良く揉んでおいて、少し編み込みを緩くしておくといいです。
ただ貼りやすくなる分、そこだけ薄くもなるので、そこは部分的な重ね貼りをしておきましょう。
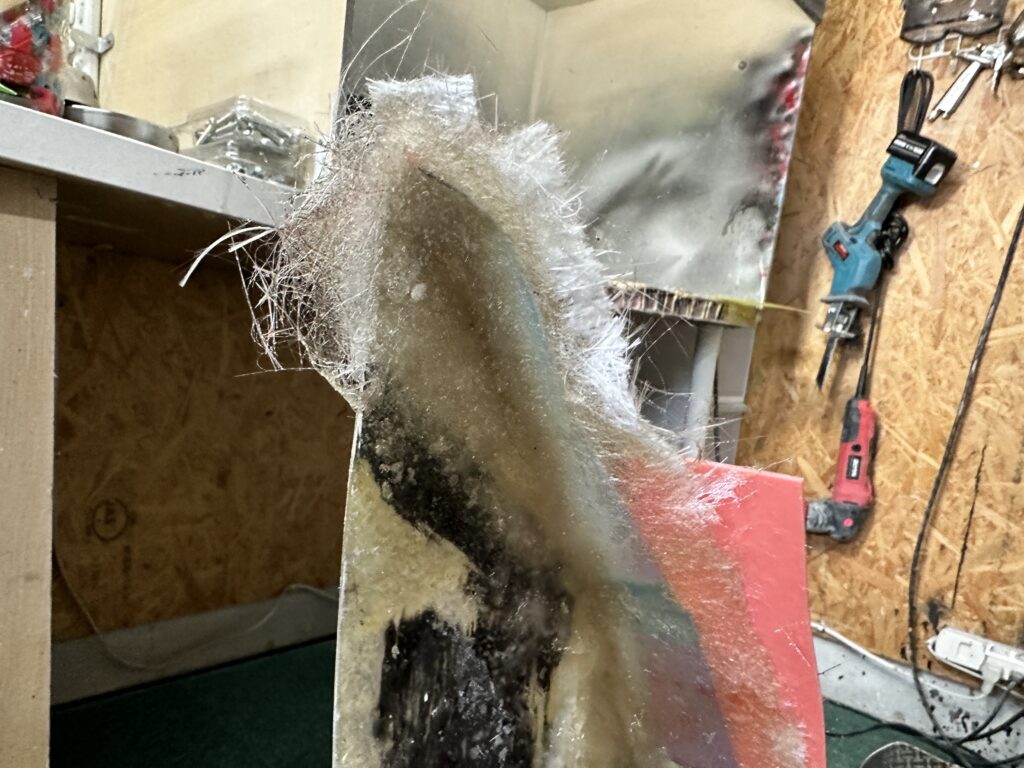
大体マットを置き終わったら、樹脂を刷毛に適量含ませて、トントントンとFRPマットを刷毛の先端で叩くように、樹脂を浸み込ませてゆきます。
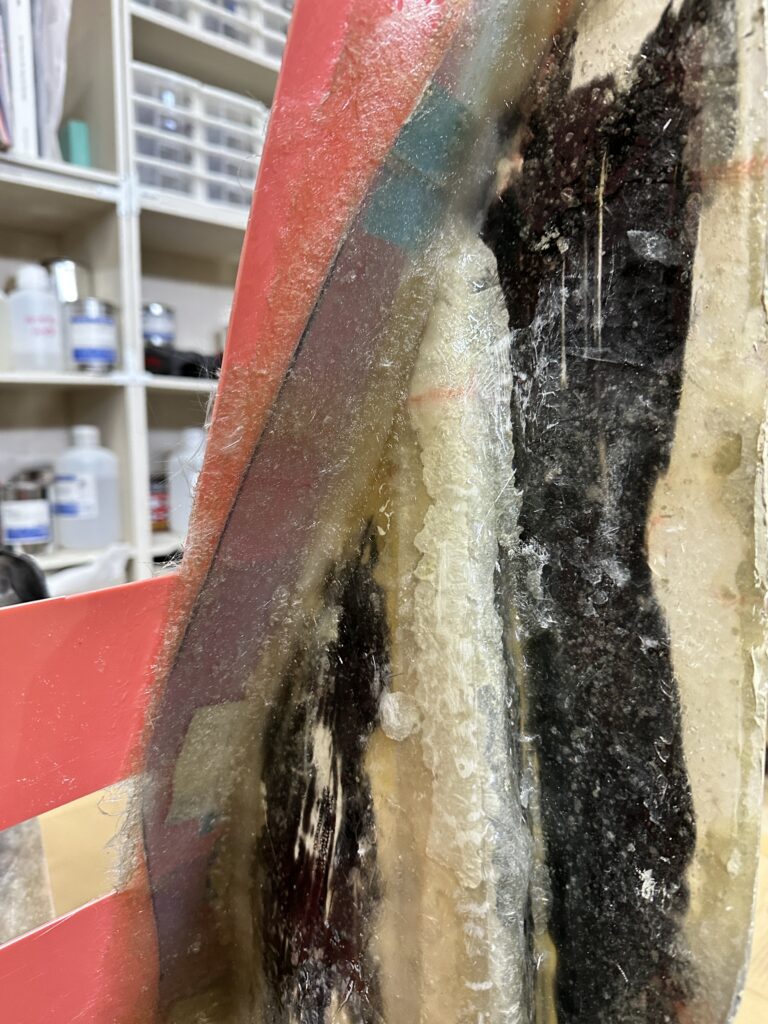
まんべんなく浸み込んで色が変わるまでやり続けますが、この際中腰になったり、変な格好で作業する事になるので結構疲れますが、休んでいる場合ではないので気合です。
臭いがきつかろうが、腰が痛かろうが、衣服が汚れようが突き進みます。
何度も分けてやったりしたら鬱になるような作業だってこともありますが、何よりも樹脂はこうしている間にも徐々に硬化反応を進めるからです。
作った樹脂が無駄にならない様にするためにも、ここは一心不乱で作業を進めます。
ヤマトさんや佐川さんが、うっかりパーツを持ってきてくれたって、この時ばかりは出ません(笑)。
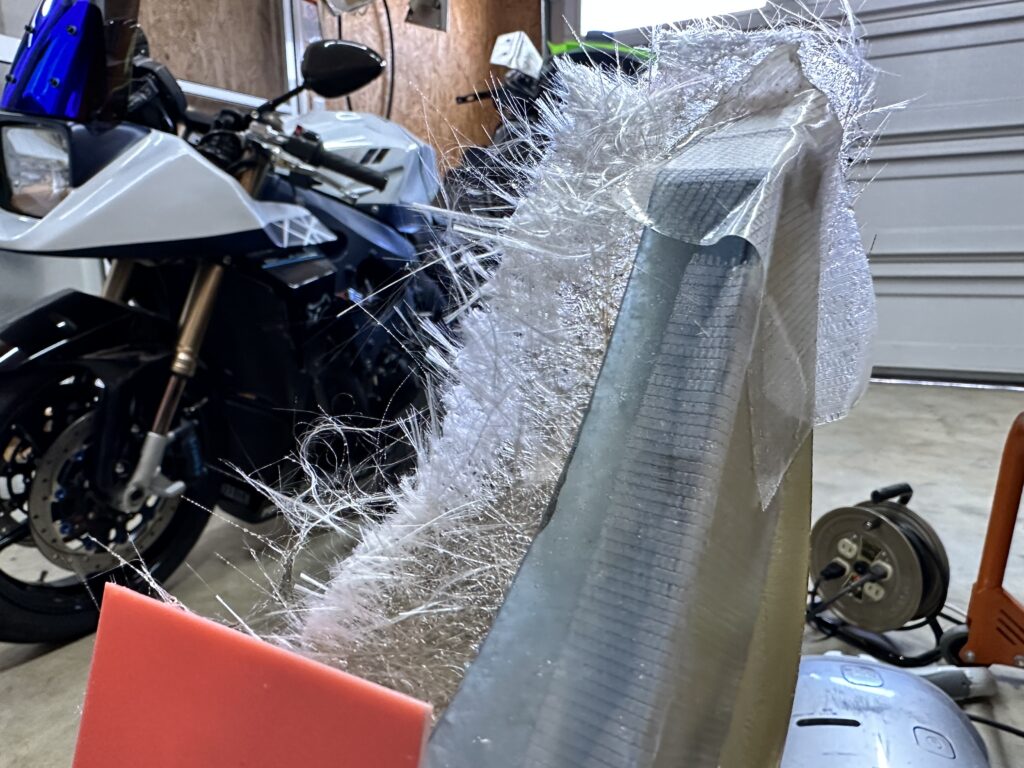
FRPは普通、はみ出すくらいに貼っておくのが普通で、硬化したら余っている部分を切ります。
プラモデルで言う「バリを取る」作業と一緒です。
なので、樹脂は馬鹿正直に全部しみ込ませなくて良いのです(重くなって剥がれてくることもある)。
そしてこの余った部分には「大事なお役目」があります。
このあまり部分を時々指で触りながら、樹脂全体の硬化具合をチェックするんです。
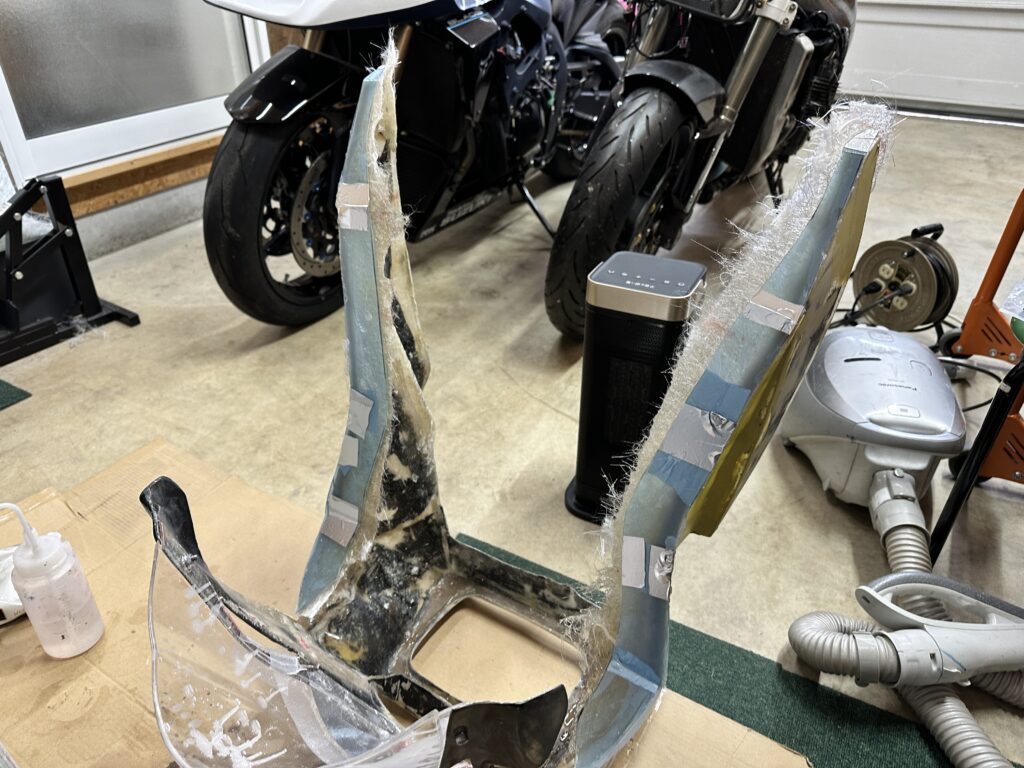
春夏秋冬の外気温や硬化剤の量で硬化時間は変わりますが、樹脂にはベタベタ→半生→カチカチの三つの形態が存在します。
その中でも「半生」状態は、作業者的にはとても価値のある状態で、ゴールデンタイムとも言えます。
半生状態は、突然訪れたかと思うと、いつの間にかカチカチに移行して行きます。
そのわずかな時間にバリ取りを行うと、カッターやハサミでサックリと綺麗に切断できるのです。
カチカチになってから同じことをやる場合は、グラインダーやベルトサンダーで、盛大に粉を巻き散らかすのですが、この半生状態であればカッターと指一本でスパッと整えることが可能です。
干し芋を手で裂くような感覚でスパスパ切れるこの瞬間を見逃すまいと、付きっきりで観察します。
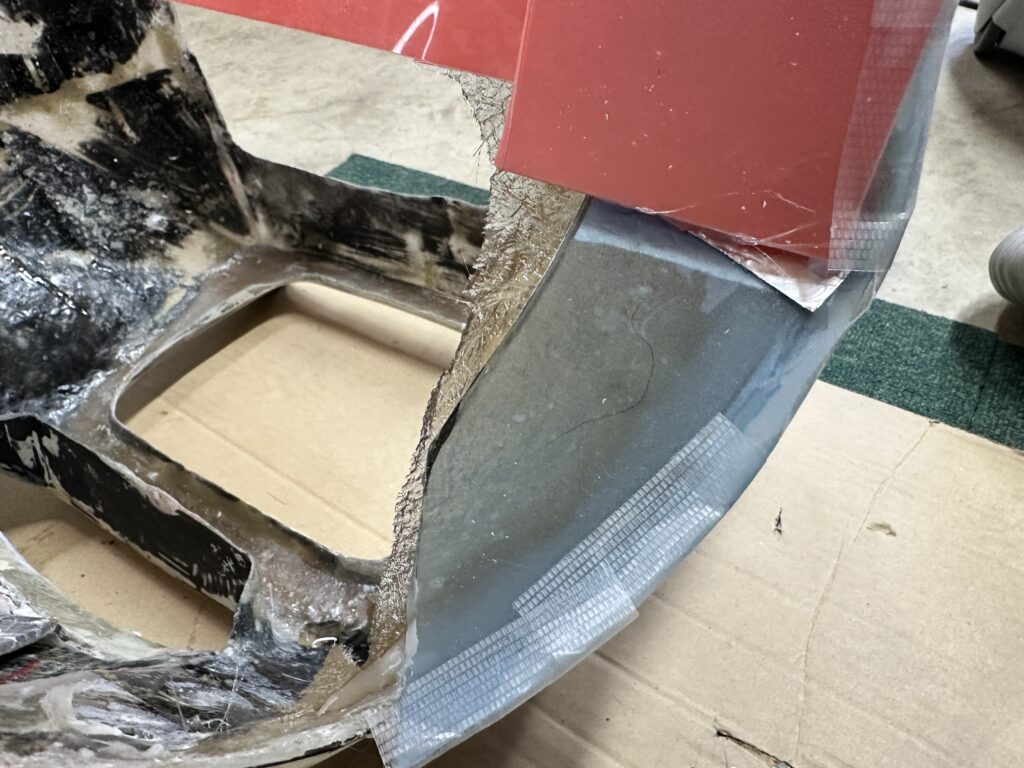
少しずつ硬化してきましたのでチョコチョコハサミで切ってみます。
まだPP板との境目部分が動くようなので一旦STOPです。
慌てて強引に切りに行くと、肝心の折り返し部分に力が掛かって歪んでしまい、本末転倒です。
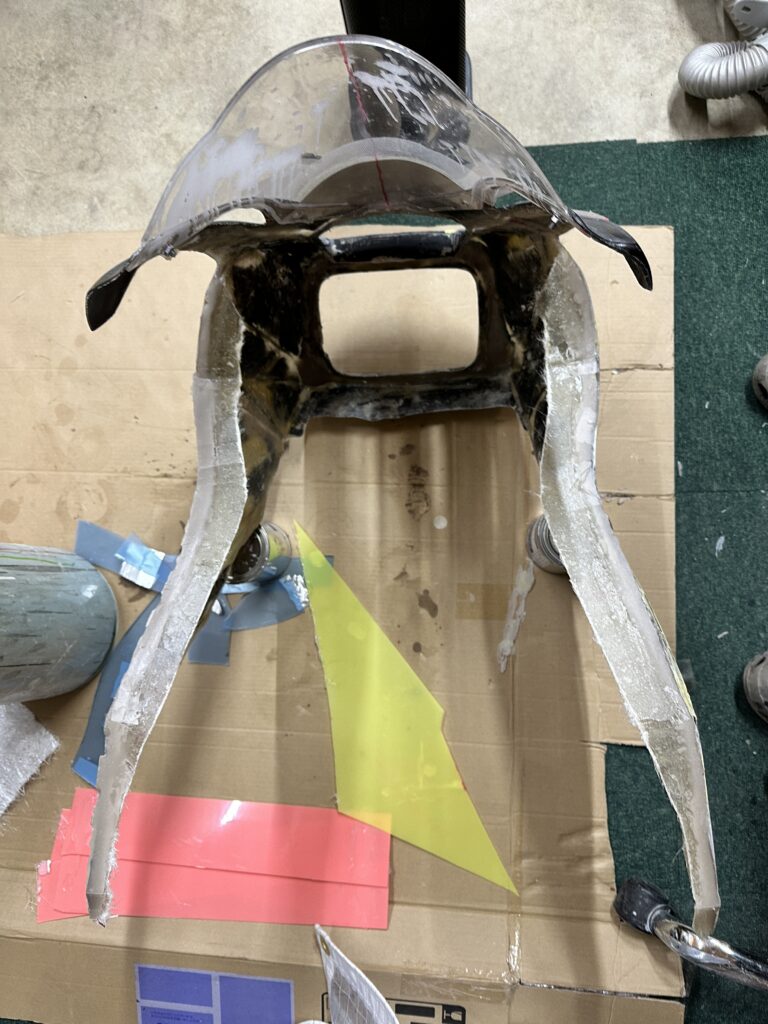
カウルは大きいので大変でしたが、完全硬化前におおよそのバリ取りが終わってしまいました。
これで一気に作業時間が短縮できるという訳です。
良かった良かった。
スクリーン追加工
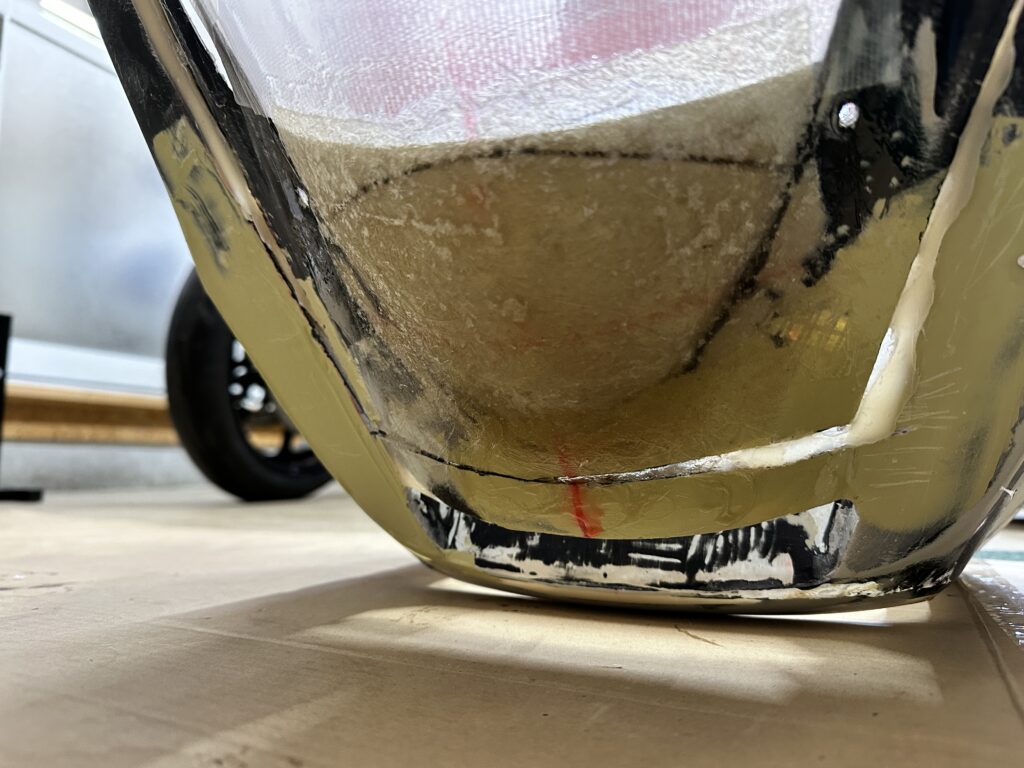
ゼッケン風デザインに変更するのと、セットされる予定の電動タコメーター裏の配線の目隠し、そして副次的にカウルの強度を確保するために、スクリーンブリッジを追加工です。
予め母体となるサンプルのスクリーンにアルミテープを貼っておき、その上から貼ります。
大きめにFRPで覆いつ、硬化後に成形して行きます。
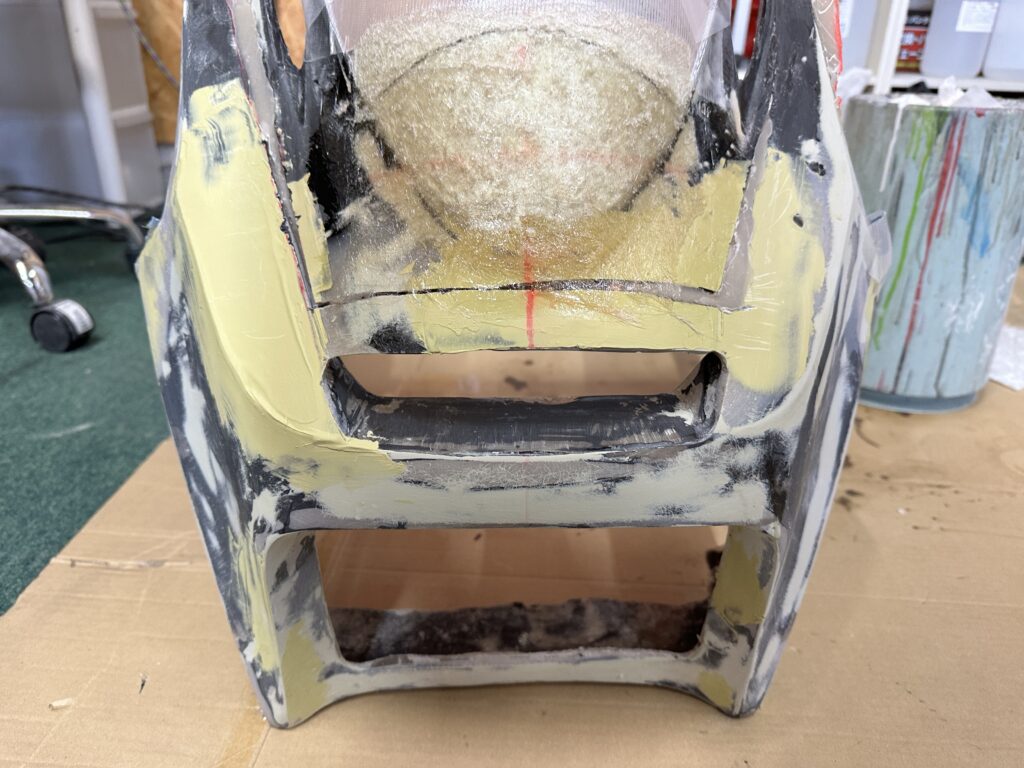
大きめにブリッジすることで、成形時の自由度が上がります。
ここは硬化後に色々とシミュレーションしてみたい部分です。
丸くしてもいいし角張ってても面白いですが、いずれにせよ「やりすぎ」ると、一気に俗っぽくなるので、そうならぬように注意です。
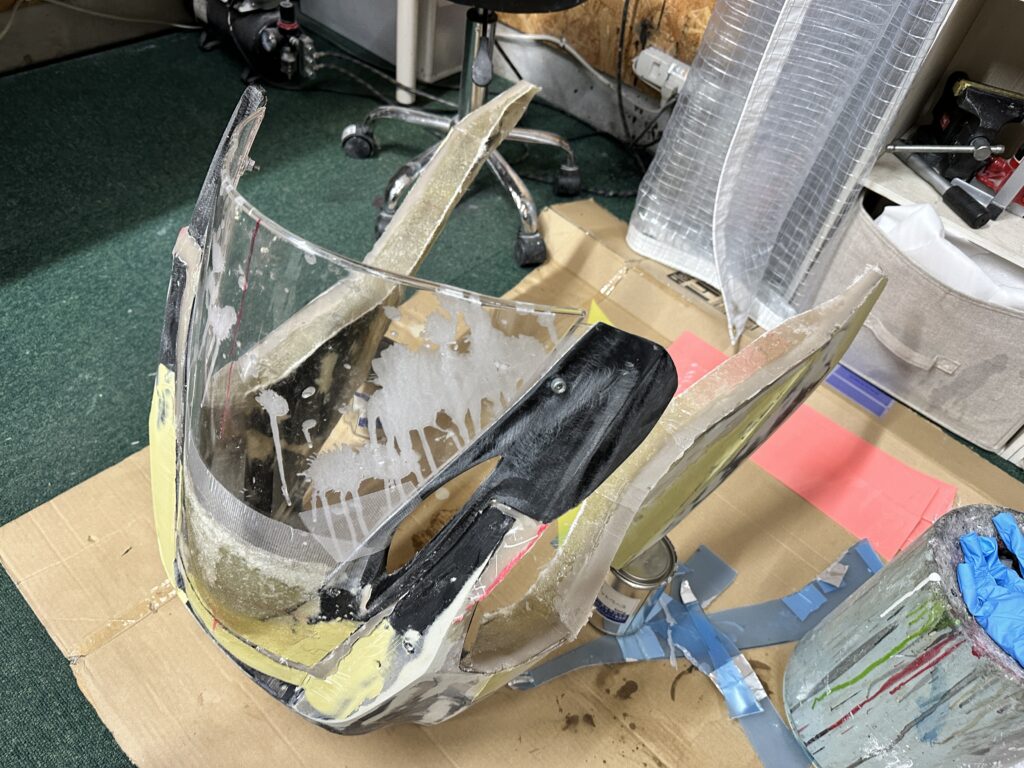
ヒーターを局所的に当てたところ以外は硬化せず、ムラができやすい冬場の作業ですが、何とか無事に折り返しまでは左右対称に成型することが出来ました。
これで一気に強度が上がったので、カウル自体の扱いが楽になります。
再びとなりますが、荒面取りと面出しに進みましょう。
予想に反して少し遠回りしましたが、アッパーカウルのマスターモデルまであと一息です。