FRP築層のあれこれ
FRP型の作成を通して、築層のウンチクを少々。
StudioQ作品は、量産性100%無視の理想造形主義なので、エッジが90度に立っていることなんて朝飯前で、酷いときは更に鋭角です(笑)。
ワンオフであることを逆手にとって、再現性など意にも介さない訳ですが、これがFRP型の作成となると、その厄災は火の粉となって、一気にわが身に降りかかります。
割り型を作る為の仕切りは直角に立てるのが基本の為、鋭角になってしまいますし、極小範囲で角張った造形が細かくされている先端部分などは、ノンパラ樹脂の粘着力をもってしても、シートの追従は期待できません。
ガラスマットは樹脂が完全に含侵してもコシがあるので、複雑な形に寄り添う事は難しく、それに加えて、完全硬化する過程で、FRPと樹脂は熱を発しながらわずかに収縮して行く特性があります。
収縮すると言う事は「動く」と言う事であり、各部を少しだけ引っ張りながら動くので、強度の無い所や複雑な形をしている所を中心に、ガラスマットが母体から離れて行きます。
樹脂を大量にマットに含ませることで重くして、離れるのを防止することも出来ますが、全てにおいてそれをやっていたら、幾ら樹脂があっても足りません。
一部離れてしまったり、気泡の様に浮いたままFRPが硬化してしまうと、製品の場合大きな巣穴となってしまい、型の場合は強度が下がります。
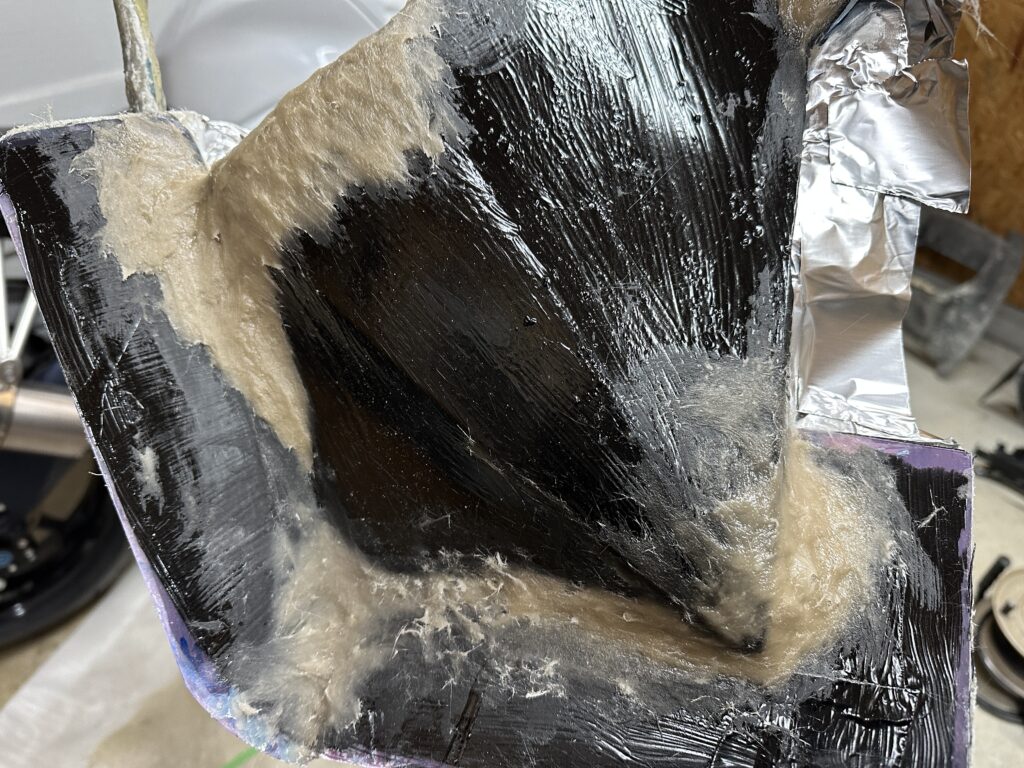
仕切りを作った隅の部分が鋭角なので、あちらこちらをパテで埋め、角を無くす必要があります。
この写真の様に、片っ端からスムーシングです。
マットが自在にうねる為の、なだらかな丘を目指します。
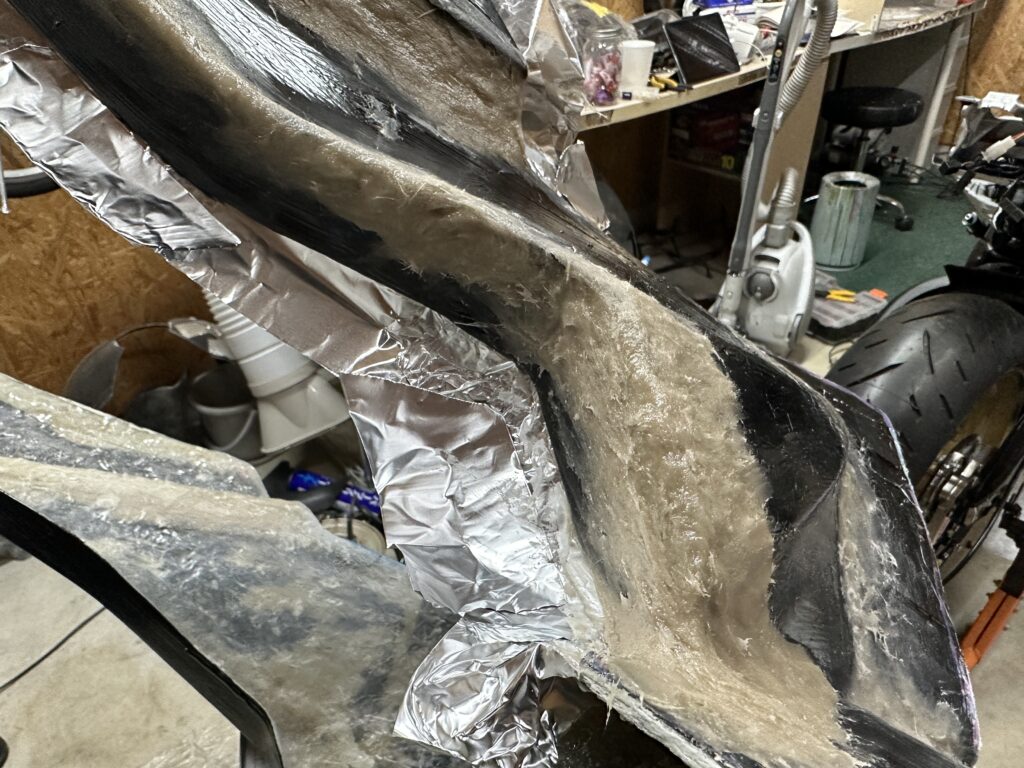
サイドの折り返しも同様です。
綺麗に90度で折りあがっている角の頂点に対して、まるでラバーエッジトリムの様に棒状にパテを伸ばしながらしがみつかせます。
出来るだけ角を打ち消し、且つ少々太らせることで、マットを直角に曲げず緩いカーブで大回りさせる方法で、何とかマットを追従させます。
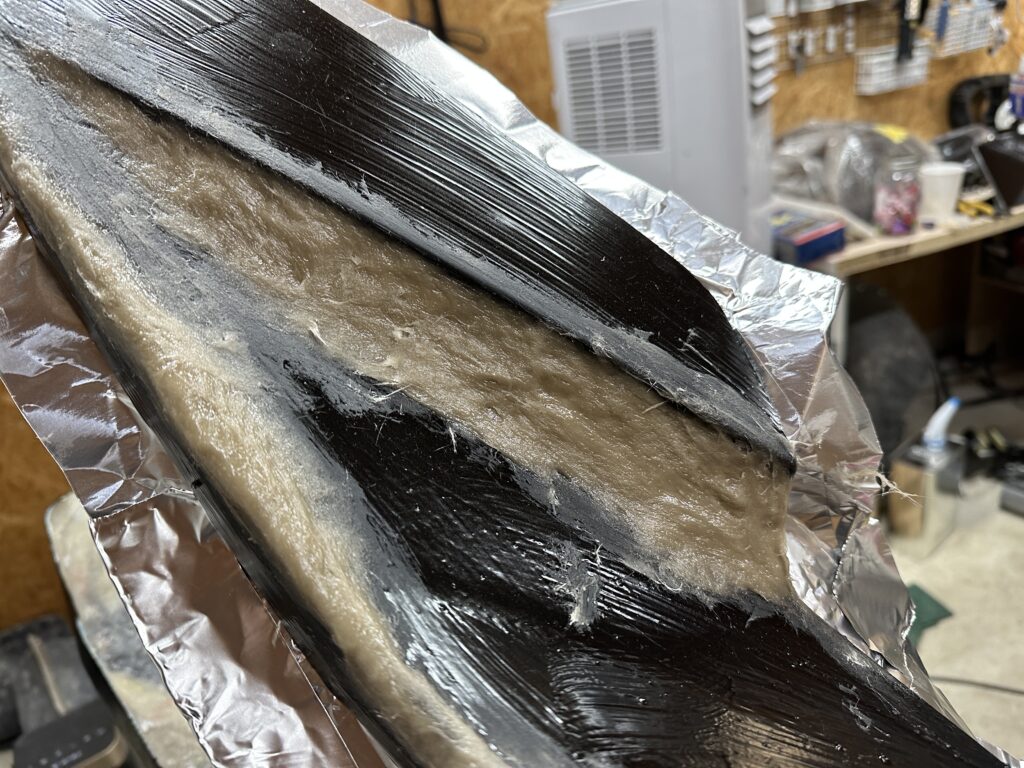
内側の折り返し部分は、大量のパテで完全に埋めきってしまい、45度まで持ってきています。
これは、マットが一回折れてから、直後に逆方向に折れる動きとなる為、ただでさえ追従しないマットが反り返るのを防ぐ為です。
このように、何十回と失敗しているからこそ分かる「あ、まずいな」と言うポイントが、幾つもあるのですが、そこはノウハウで回避します。
ガラスマットに樹脂が含侵した状態では一見OKでも、ふと目を離すと・・・マットが浮き上がってしまったり跳ね返ったりしますし、なにより手がベトベト、筆もベタベタでFRP繊維が絡みまくっています。
じぶんもマスクにゴーグルの完全装備ですから、視界も作業性もすこぶる悪い状態で、色々注意が行き届かず見落としがちです。
大型のFRP割り型作成作業は、作業に慣れている人にとっても「やりたくないこと第1位」であり、逆に言うと、これが出来たらもう何だってできてしまう「免許皆伝」です。
FRP工作には、他にも様々なテクニックがありますが、これはほんの一部にすぎません。
ここでは描ききれない、表現できないトラブルと回避方法がまだまだ存在しますが、今回はオートバイカウルの割り型作成に絞って解説・記録しておきます。
※ チャレンジしたい方は是非参考にしてください
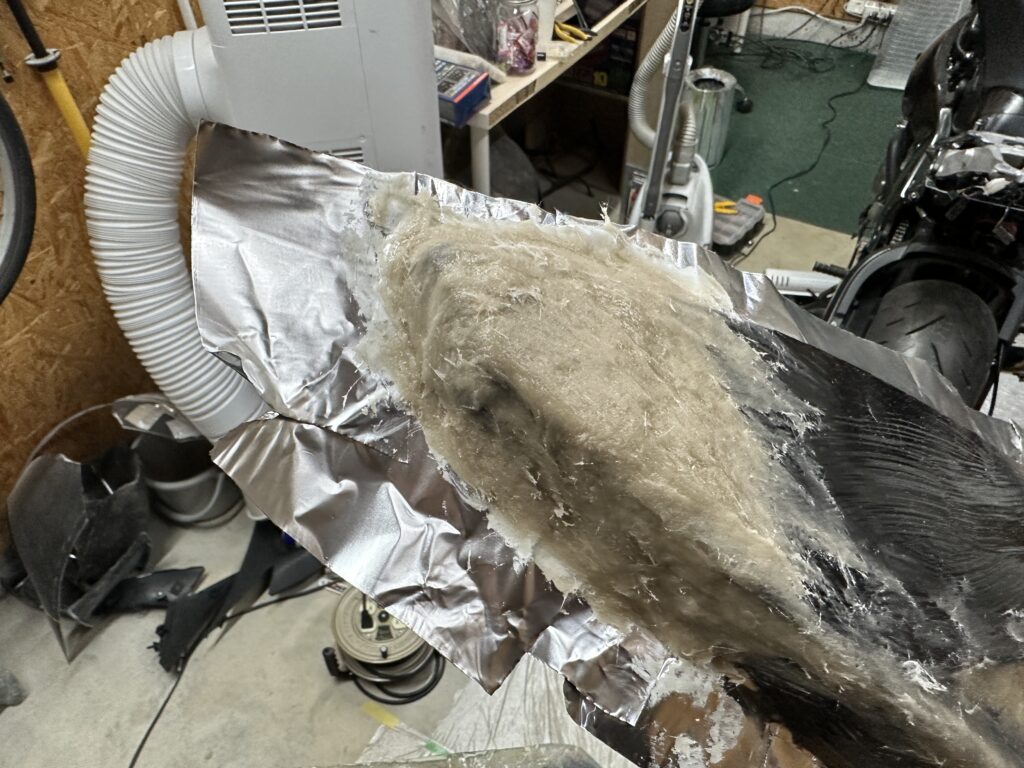
このようなカウルの先端部分などは、絆創膏の様なマットを作って「×」の字に折り重ねることで包み込むことも可能ですが、うっかりするとマスターモデルの裏側まで樹脂が回り込んでしまい、ガッチリとカウルを掴んで(食って)しまいます。
そうなったら、もう抜けなくなってしまうばかりか、今度は型まで壊れかねませんので、あまりお勧めできません。
これらを回避すべく、先んじてパテで丸く包み込むことで、マットが定着しやすくしておきます。
パテもそうですが、築層時に樹脂がカウル裏に回らないように、強粘着のアルミテープで周囲を防御しています。
Before/After
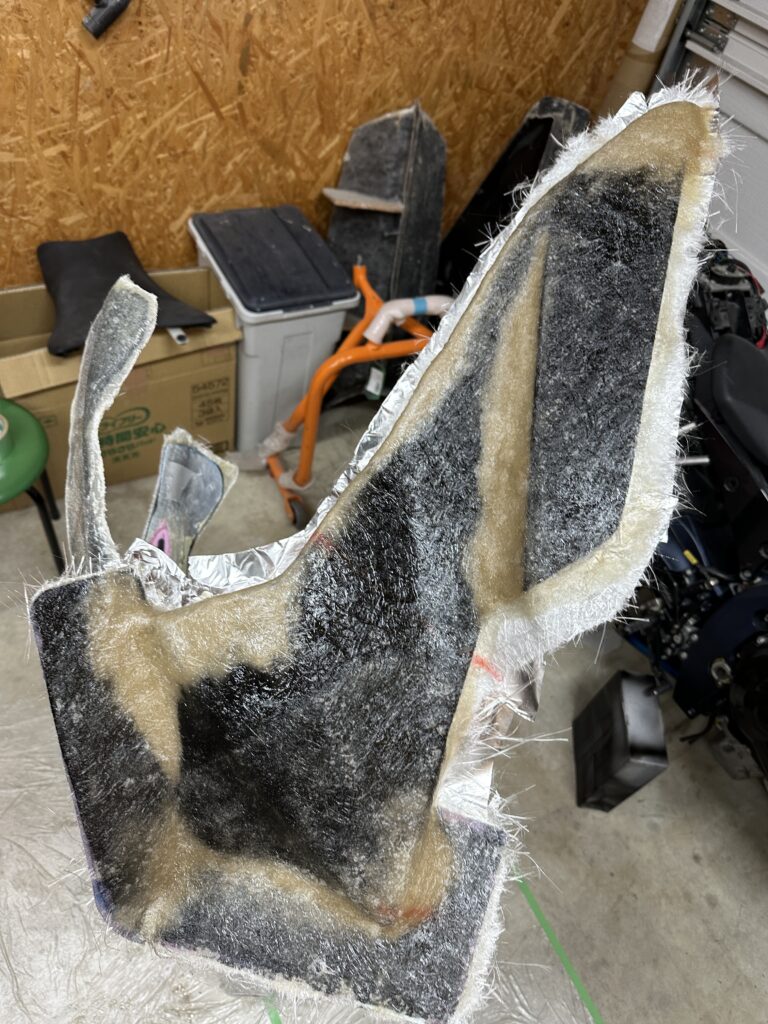
これは#450のガラスマットをたった一枚張っただけの状態です。
下準備のおかげで、とてもきれいに貼ることが出来ました。
多層築層のコツは、最初の1層を貼ったら少し待つことです。
最初の1層が硬化して動かなくなってから、それ以降の層を一気に貼って行きます。
そうすることで、多層築層時に自重による動きや剥がれを防止します。
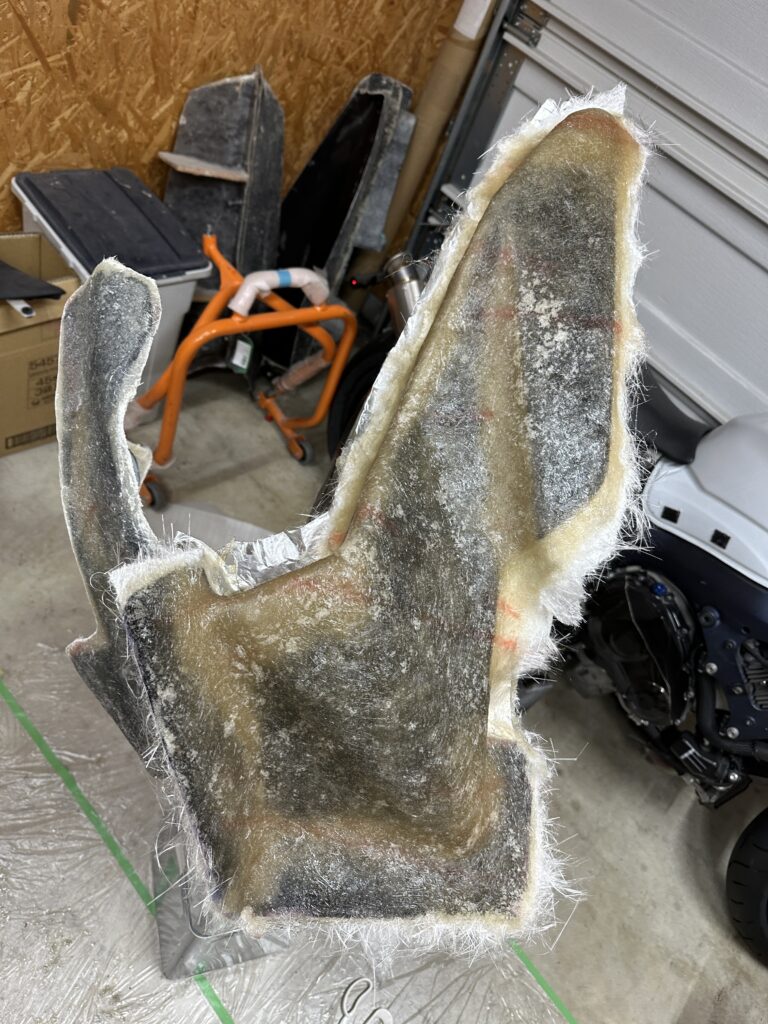
これが10層重ねた状態です。
大量の樹脂を食らい、大分重くなっています。
硬化の過程で発生する、生乾きの僅かな時間を狙って、不要部分をカッターでサッと切り落としておくと、この後の作業が大変楽になります(今回は見逃しましたw)。
春先は気温が上がるので、冬場に比べてFRPの効果速度(反応速度)が一気に上がります。
硬化剤の量をかなり抑え、反応を抑えながら一気に築層を進めます。
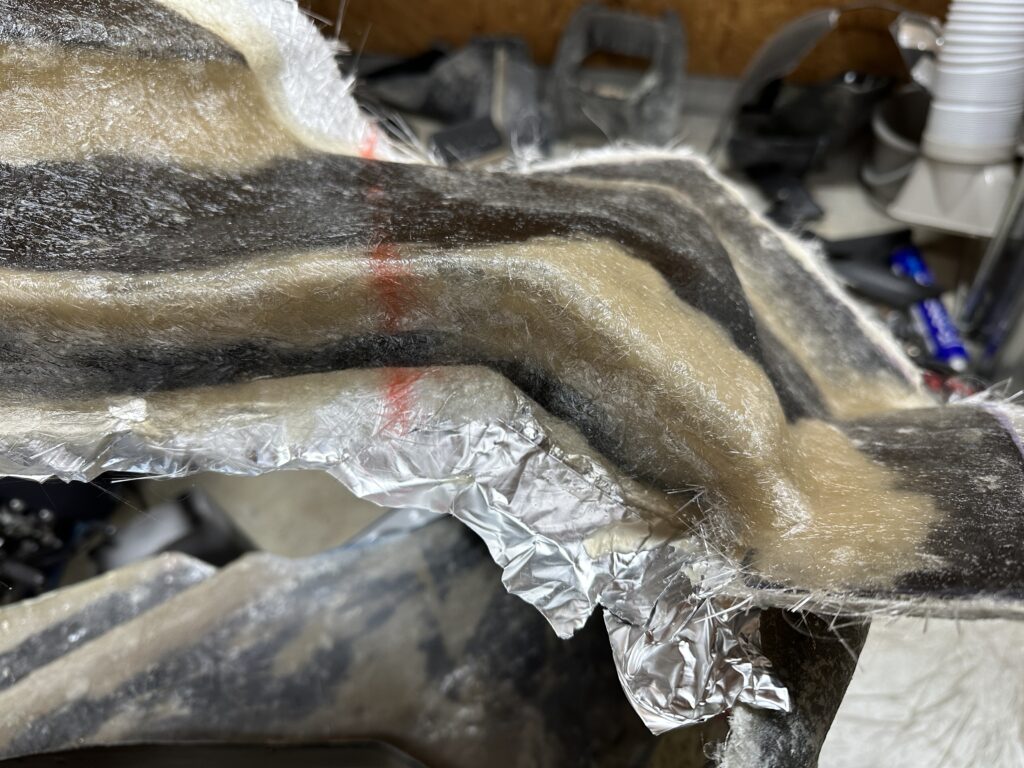
角の部分にしがみつかせたパテに対して、1層目です。
僅かに浮きがあったので、この後樹脂を追加して塗布することで、完全に掴ませました。
ここまで準備しておいてもこの有様ですから、まったく油断も隙もありません・・・・。
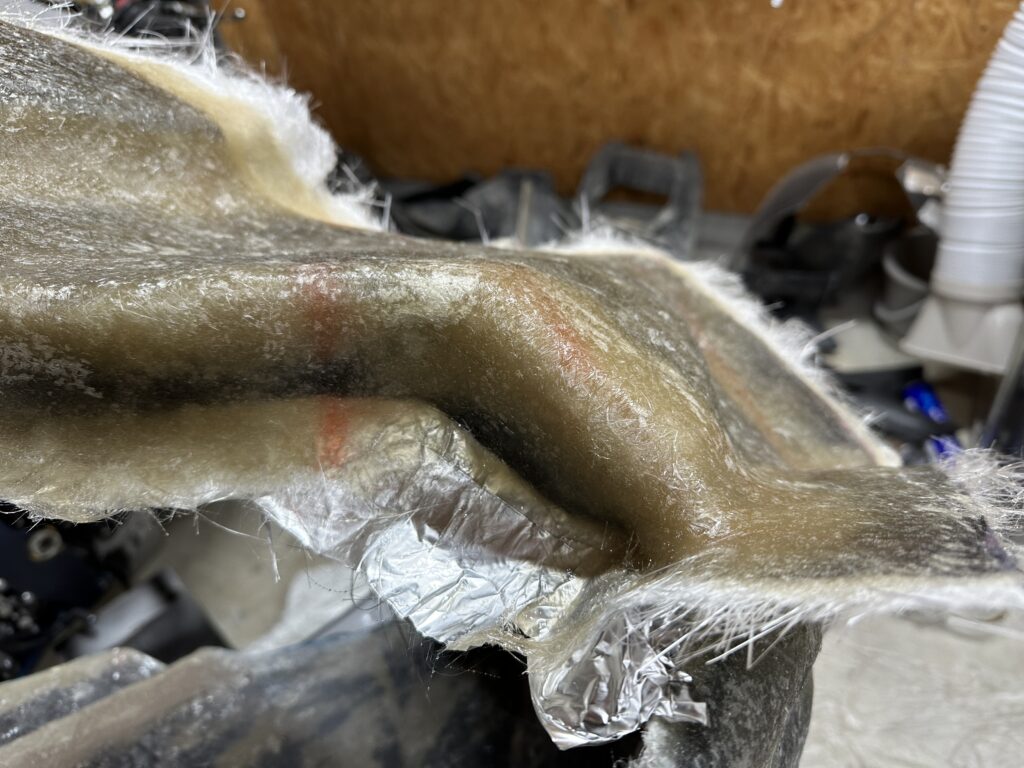
なんとかかんとか誤魔化しながら約10層の築層を完了です。
長時間の中腰作業+おそらく有毒であろう強い異臭との闘いです(←目にも染みるレベル)。
普通に考えて、住宅密集地でやるような作業ではありません。
硬化に掛かる半日の間もずっと刺刺激臭を放っており、ご近所からクレームも来るのは避けられません。
作業環境に強力な換気施設がない限り確実に健康を害してしますし、防毒マスクや安全ゴーグル、ツナギや手袋などの装備も必要なので、くれぐれも準備・確認をしてください(笑)。
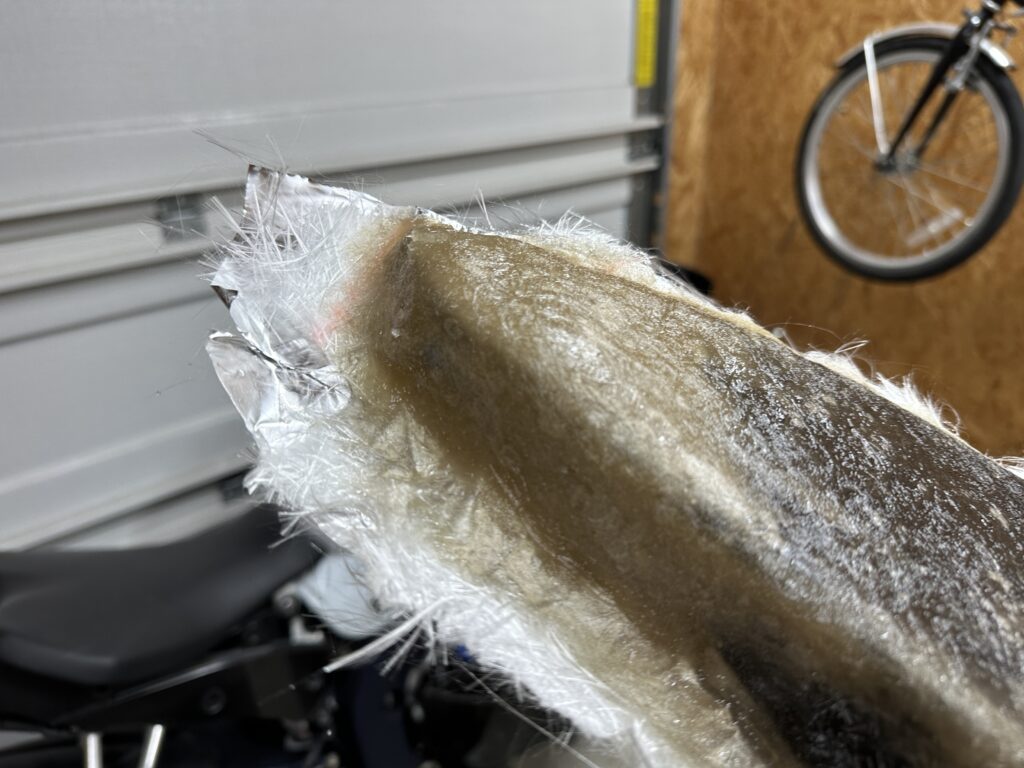
これは、よく離れてきてしまって失敗する先端部分の1層目です。
マットをかなりほぐしてあるので何とかなりましたが、ギリギリでした(その分薄くなる)。
あまり強度が出ないので、大きめに作っておいて、硬化後に不要部分を切断して綺麗にします。
製品を型から抜く際には棒やヘラでかなり強く抉ったりするのですが、こういった繊細な部分は、その際アッサリと欠けてしまいます。
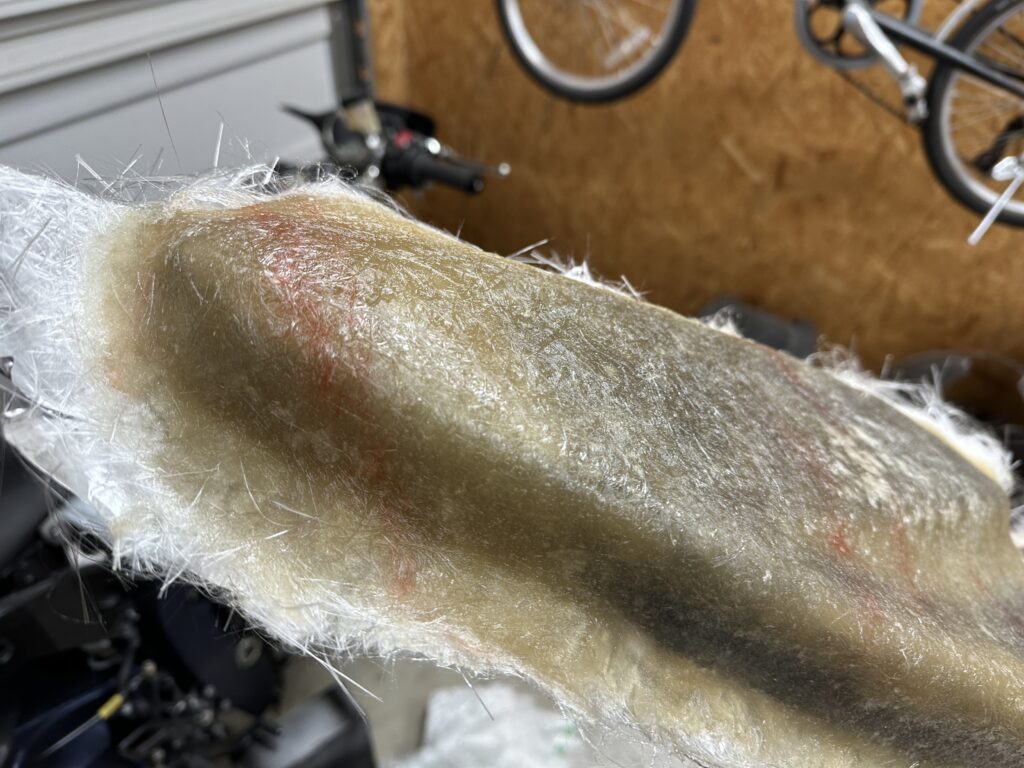
1層目のマットが動かない事を確認した後に、どんどん築層して自重で動かなく固定します。
築層すればするほどエッジが丸くなってゆくので貼りやすくなります。
しかし・・・・・やれどもやれども、型はまだまだ出来ません。
FRP樹脂は、硬化剤を入れた瞬間から科学反応が進んでいってしまうので、間に休憩を挟むことも出来ない為、過酷です(笑)。
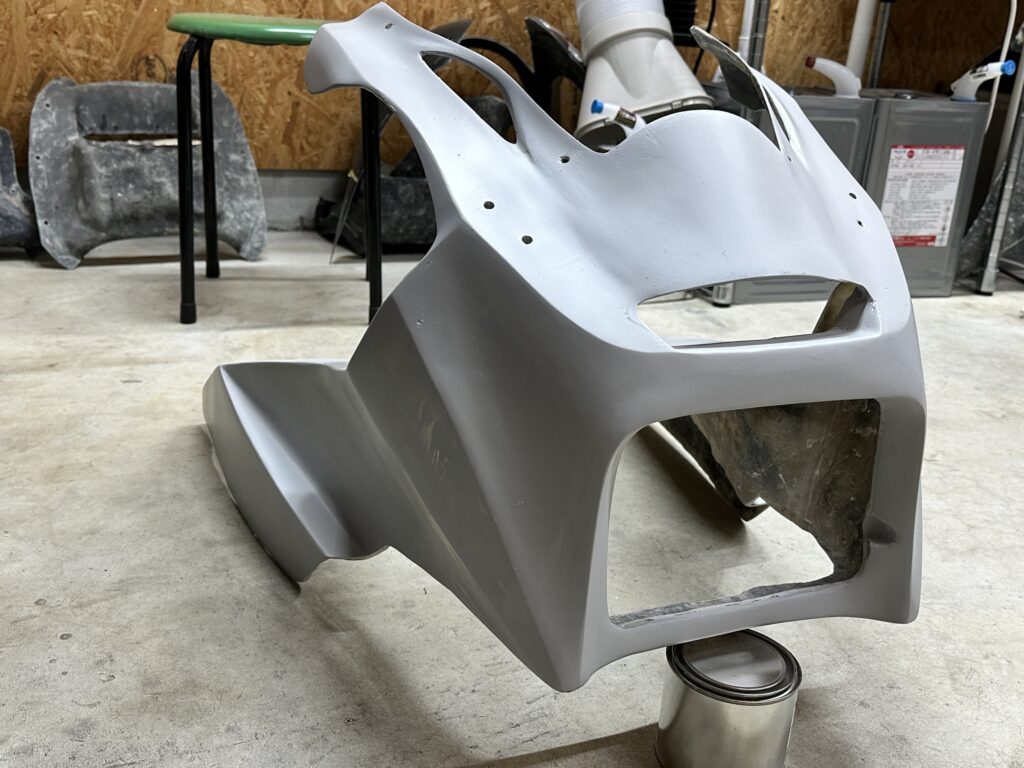
一般的にこの作業を、プロにデザインから相談し、CADや3Dプリンターなどでマスターモデルを作成してもらい、そこから型を起こしてから製品の射出までを依頼すると、バイクパーツ一つ辺りの相場は35万円位~です(車のエアロパーツのような大型な物は60万円~が相場です)。
私の様に経験を積み、DIYでやることもできますが・・・・・手作業なので膨大な月日が掛かります。
そもそも始めたきっかけは、お金が無かったこともありますが、それよりも「自分の理想の形」を口伝で100%他人に伝えるなど、現実的では無いと感じたからです。
誰かにお任せするのも悪くないのかもしれませんが、私の場合とてもストレスを感じます。
私はそれがどうしても受け入れられなかったので、敢えてDIYを選んだのかもしれません。
デザインの検討から成形(そして修正)、製品の塗装から車両へのフィッティングまで!
結局納得が行くまで、全て自分の手でやることに拘りました。
これがStudioQの発足の原点なんだな・・・と改めて思いますし、逆にこの拘りがなくなってしまった時、もしくは何らかのそれに近い感覚を覚えたときは、このプロジェクトを終了する時だと思っています。
始まりがあれば、終わりもあるものです。
沢山の方々に私の作品を愛して頂き、ここまでやってこれたことに大変感謝していますが、そろそろ終り方を考えるべき時期に来ていると感じています。